Kimya ve Seramik Üretimi hakkında tüm detayları öğrenin! Seramik malzemelerinin üretim süreci nasıl gerçekleşir? Kimya endüstrisi nasıl işler? Teknoloji ve yenilikler nelerdir? Sorunların çözümü için doğru yerdesiniz
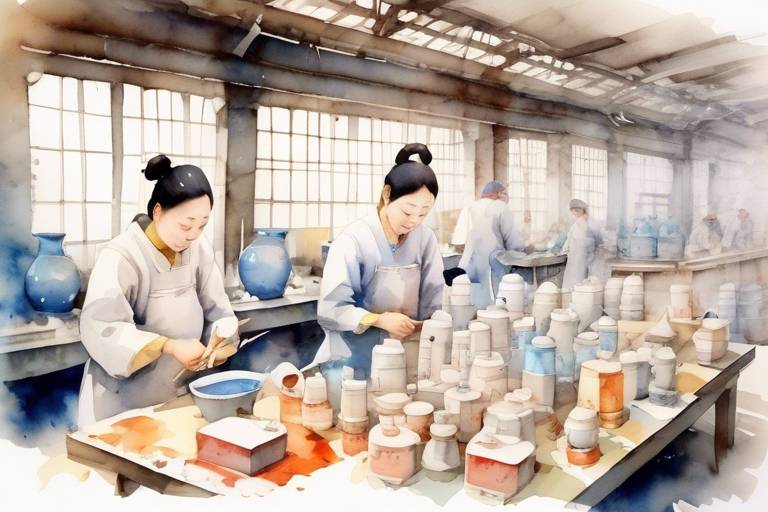
Bu makalede kimya ve seramik üretimi hakkında genel bir bakış sunulacaktır. Kimya ve seramik endüstrileri, dünya genelinde oldukça yoğun bir biçimde kullanılan malzemelerin üretiminde yer alan büyük endüstriyel sektörlerdir. Kimya endüstrisi, temel kimyasalların, plastiklerin, gübrelerin, ilaçların ve diğer birçok malzemenin üretiminde kullanılırken, seramik endüstrisi ise porselen, seramik karo, çömlek ve cam eşyaların üretiminde kullanılır.
Kimya ve seramik endüstrilerinde kullanılan malzemeler ise oldukça çeşitlidir. Kimya endüstrisinde kullanılan malzemeler, hammaddeler, laboratuvar kimyasalları, solventler ve reaktifler gibi ürünlerdir. Seramik endüstrisinde ise kil, cam, frit, refrakter malzemeler, pigmentler, yardımcı malzemeler ve glazürler gibi malzemeler kullanılır.
Seramik ve Kimya Endüstrisi
Seramik ve kimya endüstrisi, geniş bir alana yayılan sanayi sektörleridir. Bu sektörlerin ana hedefi, ham maddeleri işleyerek yeni malzemeler üretmek ve bu malzemeleri çeşitli sektörlere satarak gelir elde etmektir.
Seramik endüstrisi, farklı amaçlar için kullanılan çeşitli seramiklerin üretimini içerir. Bunlar çimento, cam, kil, porselen, fayans ve seramik karolar gibi ürünleri kapsamaktadır. Kimya endüstrisi ise, her türlü kimyasal maddelerin üretimini içerir. Bu maddeler arasında ilaçlar, temizlik maddeleri, kozmetik ürünler, boya ve kimyasal gübreler de yer alır.
Endüstride Kullanılan Malzemeler | Amaçları |
---|---|
Cam | Farklı sektörlerin kullanımı için pencere, mobilya gibi eşyalar üretmek |
Kil | Çanak çömlek, fayans gibi dekoratif eşyaların üretimi |
Porselen | Lüks porselen takım gibi özel ve özgün ürünlerin üretimi |
Çimento | Inşaat, yol, köprü, baraj inşaatı gibi yapı projelerinde kullanılır |
Temizlik maddeleri | Kir, leke, mikrop gibi zararlı maddelerin yok edilmesi için kullanılır |
İlaçlar | Farklı hastalıkların tedavisi için üretilir |
Kimya ve seramik endüstrisi, dünya genelinde ekonomik olarak önemli bir yere sahiptir. Bu endüstri dallarında çalışanlar yüksek gelir elde edebilirler ve kariyerlerinde başarılı yükselişler kaydedebilirler.
Kimya Endüstrisinde Üretim Süreci
Kimya endüstrisi, birçok farklı ürünü üretmek için kullanılan uzun ve karmaşık bir süreçtir. Kimya endüstrisinde üretim süreci, kimyasal reaksiyonlar ile doğal ve sentetik malzemelerin dönüştürülmesini içerir.
Bu dönüşüm süreci, endüstriyel ölçekte gerçekleştirilir ve genellikle yüksek sıcaklık ve basınç altında gerçekleşir. Kimya endüstrisinde, üretim süreci için çeşitli yöntemler kullanılır:
- Distilasyon: Bileşenlerin ayrılması amacıyla kullanılan bir yöntemdir.
- Ekstraksiyon: Sıvıların veya katıların birbirinden ayrılmasını sağlayan bir tekniktir.
- Kristallizasyon: Sıvı bileşenleri kristal haline getirerek ayırma yöntemidir.
- Filtrasyon: Katı ve sıvı bileşenlerin birbirinden ayrılmasına olanak tanıyan bir yöntemdir.
Ayrıca, kimya endüstrisinde üretim süreci, katalizörlerin kullanımı ile de gerçekleştirilebilir. Katalizörler, kimyasal reaksiyonların hızını artıran ve ürünlerin verimliliğini maksimize eden maddelerdir. Katalizörler, reaksiyonun hızını artırmak için kullanılan biyolojik bireyler veya kimyasal maddeler olabilir.
Tüm bu yöntemler, kimya endüstrisinde üretim sürecini daha verimli ve etkili hale getirmek için kullanılır.
Katalizörler ve Reaksiyonlar
Kimya endüstrisinde, özellikle organik kimyada, reaksiyon hızlarını arttırmak için katalizörler kullanılır. Katalizörler, kimya reaksiyonlarını etkileyen ve yeniden düzenleyen maddelerdir. Böylece, reaksiyon hızı artar ve istenilen sonuç daha hızlı elde edilir. Katalizörler, kimyasal yapılarına bağlı olarak, birçok farklı reaksiyonu hızlandırabilirler.
Katalizörler, genellikle metal iyonları, kompleksler veya organik moleküllerdir ve katalizör türleri arasında en yaygın kullanılanlar platin, nikel, paladyum ve rutenyumdur. Katalizörler, reaksiyon ortamına katılabileceği gibi ayrı olarak da kullanılabilir. Bu katalizörler, reaksiyonun gerçekleştiği yere bağlanır ve reaksiyonun hızını arttırırlar. Bu sayede, daha az enerji gerektiren daha verimli bir reaksiyon gerçekleştirilir.
Katalizörlerin kullanımı, birçok bileşiğin, özellikle organik bileşiklerin, daha verimli bir şekilde üretilmesine yardımcı olur. Bu reaksiyonlar, genellikle endüstriyel ölçekte gerçekleşir ve genellikle katalizörlerin kullanılması, reaksiyon hızını arttırarak üretim süresini kısaltır ve maliyetleri düşürür.
Katalizör Türleri
Kimya endüstrisindeki reaksiyonların hızlandırılmasında katalizörler çok önemlidir. Farklı kimyasal reaksiyonlar için farklı katalizörler kullanılır ve çeşitli katalizör türleri vardır. Katalizörler, reaksiyonlarda kullanılan hammaddelerin miktarını azaltarak ve ürün verimliliğini artırarak, reaksiyonların hızlandırılmasına yardımcı olurlar.
Katalizör türleri aşağıdaki listede verilmiştir:
Katalizör Türleri | Reaksiyonlar |
---|---|
Asit Katalizörleri | Polimerizasyon, Dehidrasyon |
Metal Katalizörleri | Oksidasyon, Redüksiyon, Hidrojenasyon, Karbonilasyon |
Gaz Katalizörleri | Dönüşüm, Hidrojenasyon, Oksidasyon |
Selektif Katalizörler | Farklı çeşit reaksiyonlar için kullanılır. |
Asit katalizörleri, dehidrasyon ve polimerizasyon gibi reaksiyonlarda etkilidir. Metal katalizörleri, oksidasyon, redüksiyon, hidrojenasyon ve karbonilasyon gibi reaksiyonlar için kullanılır. Gaz katalizörleri ise dönüşüm, hidrojenasyon ve oksidasyon gibi reaksiyonlarda kullanılır. Seçici katalizörler, farklı çeşit reaksiyonlar için kullanılır ve özellikle aralıklı reaksiyonlarda etkilidir. Hangi katalizörün hangi reaksiyon için kullanılacağı, endüstriyel uygulamalar yapılarak belirlenir.
Reaksiyon Tasarımı
Kimya endüstrisi, birçok farklı reaksiyonun gerçekleştirilmesini gerektirir. Reaksiyon tasarımı, bir reaksiyonun verimliliğini, seçiciliğini ve hızını artırmaya çalışan bir disiplindir. Bu süreçte tasarım, reaksiyonun nasıl çalıştığına, ne tür katalizörlerin kullanılacağına ve diğer faktörlere karar verir.
Bu tasarımın başarısında katkısı olan birçok faktör vardır. Öncelikle, kimyasal kinetiği anlamak ve reaksiyonun hızını ve seçiciliğini artırmak için tasarım yapmak önemlidir. Ayrıca, reaksiyonun gerçekleştirileceği ortam ve malzemeler de tasarımın önemli unsurlarından biridir.
Reaksiyon tasarımı için kullanılan birçok araç vardır. Örneğin, matematiksel modeller, reaksiyon koşullarını öngörür ve en iyi sonuçları elde etmek için reaksiyon değişkenlerini optimize etmek için kullanılır. Diğer araçlar arasında, kullanılan katalizörlerin seçimi, reaksiyonun gerçekleştirileceği ortamın seçimi ve reaksiyona dahil olan tüm malzemelerin optimizasyonu yer alır.
Bu tasarım süreci, kimya endüstrisi için son derece önemlidir. Reaksiyon tasarımı sayesinde endüstri, daha yüksek verimlilik, daha az kaynak kullanımı ve daha az atık üretimi sağlayabilir. Ayrıca, daha iyi tasarlanmış reaksiyonlar, daha yüksek kaliteli ürünler ve daha az işletme maliyeti anlamına gelir.
Malzeme Karakterizasyonu
Malzeme karakterizasyonu, malzemelerin fiziksel ve kimyasal özelliklerini ölçmek ve analiz etmek için kullanılan bir yöntemdir. Bu yöntem, malzemelerin özelliklerini anlamak, performanslarını değerlendirmek ve hangi uygulamalara uygun olduklarını belirlemek için kullanılır.
Malzeme karakterizasyonu, malzemelerin özelliklerini ölçmek için çeşitli teknikler kullanır. Bu teknikler arasında x-ışını difraksiyonu, spektroskopi, mikroskopi, termal analiz, manyetik özelliklerin ölçümü ve mekanik özelliklerin test edilmesi yer alır. Bu teknikler, malzeme özelliklerinin tamamını ölçemez, ancak birçok önemli özellik hakkında bilgi sağlar.
Örneğin, x-ışını difraksiyonu, kristal yapıları hakkında bilgi verirken, spektroskopi, malzemelerin molekül yapıları ve bileşenleri hakkında bilgi sağlar. Mikroskopi, malzemelerin yüzey özelliklerini ve yapılarını gözlemlemek için kullanılırken, termal analiz, malzemelerin sıcaklığa ve ısıya tepkileri hakkında bilgi verir. Manyetik özelliklerin ölçümü, malzemelerin mıknatıslanma özellikleri hakkında bilgi sağlar. Mekanik özelliklerin test edilmesi ise malzemelerin dayanıklılığı, çatlama direnci ve esnekliği hakkında bilgi verir.
Bu ölçümler ve analizler, endüstride malzemelerin sürekli olarak geliştirilmesi ve iyileştirilmesi için önemlidir. Malzemelerin kalitesini artırmak, süreçleri optimize etmek, kaynakları en iyi şekilde kullanmak ve yenilikleri keşfetmek için malzeme karakterizasyonu süreci büyük bir önem taşır.
Seramik Üretim Süreci
Seramik üretimi, kil veya toprak gibi mineral malzemelerin işlenmesiyle gerçekleştirilir. İlk adım olarak, toprak veya kil benzeri malzemeler doğal bir yolla çıkarılır veya endüstriyel olarak üretilir. Ardından, bu malzemeler öğütülür ve özel bir karışıma dönüştürülür. Bu karışımın içindeki malzemeler, seramiklerin özelliklerine göre değişebilir.
Üretim sürecinin bir sonraki adımı olan şekillendirme işlemi, toprak karışımının belirli bir şekilde kalıplanmasıdır. Bu işlem sırasında, özellikle ince detayların yerine getirilmesi için enjeksiyon kalıplama yöntemi veya sınır alanı yöntemi gibi özel teknikler kullanılabilmektedir. Daha sonra, seramiklerin sertleşmesi için fırınlama işlemi gerçekleştirilir. Bu işlem sırasında, seramiklerin sertliği ve yoğunluğu artar. Son adımda, boyama veya pürüzlendirme gibi değişik işlemler uygulanabilir.
Seramikler geniş bir şekilde kullanılır ve inşaat, gıda, tıp, savunma sanayi ve hatta uzay araştırmaları gibi birçok endüstride önemli bir malzeme olarak kabul edilir. Çanak çömlek ve vazolar gibi dekoratif ürünlerden, döşeme ve mutfak gereçleri gibi günlük kullanım eşyalarına kadar, seramikler hayatımızın birçok farklı alanında karşımıza çıkar.
Bileşenler ve Malzemeler
Seramiklerin üretiminde kullanılan bileşenler arasında kil, feldispat, kuvars ve kaolin bulunur. Bu malzemeler seramik üretiminde en sık kullanılan hammaddelerdir.
Kil, seramiklerin ana bileşenidir. Seramik kilinin özellikleri, içerdiği mineraller ve şekillerine göre değişir. Feldispat, kuvars ve kaolin ise seramiğin özelliklerini geliştirmek ve dayanıklılığını artırmak için kullanılır.
Bunun yanı sıra, seramik üretiminde kullanılan malzemeler arasında cam, metal oksitler, boratlar ve nükleer atıklar da yer almaktadır. Bu malzemeler, seramiğin dayanıklılığını, sıcaklık toleransını ve parlaklığını artırmak için kullanılır.
Seramik üretiminde kullanılan malzemelerin özellikleri de önemlidir. Örneğin, kilin plastiği, işlenebilmesini ve şekillendirilmesini kolaylaştırırken, feldispat seramiği daha dayanıklı hale getirir. Kuvars, seramiğin şeffaflığı ve sertliğini artırırken, kaolin ise beyaz renk verir ve seramiklerin pürüzsüz bir yüzey oluşturmasına yardımcı olur.
Üretim Yöntemleri
Seramik üretimi, farklı yöntemlerle gerçekleştirilebilir. Her bir yöntemin kendi avantajları ve dezavantajları vardır. Bunlardan bazıları aşağıda açıklanmaktadır:
1. Basınçlı Kalıplama: Bu yöntem, seramik üretiminde en yaygın kullanılan yöntemlerden biridir. Hamurun kalıplama makinesine yerleştirildiği ve daha sonra yüksek basınç altında kalıplara sıkıştırıldığı bir süreçtir. Bu yöntemle kaliteli ve doğru boyutlarda seramikler üretilebilir. Ancak, yüksek basınç altında olmak, bazen malzemenin sertleşmesine neden olabilir ve üretim süreci karmaşık hale gelebilir.
2. Sınır Alanı Yöntemi: Bu yöntemde, seramik hamurunun iki farklı malzeme arasında sıkıştırılmasıyla seramikler oluşturulur. Bu yöntemin kullanılması, ince ve hassas seramikler oluşturmak için idealdir. Ancak, üretim süreci daha uzun sürebilir ve maliyeti artırabilir.
3. Enjeksiyon Kalıplama: Bu yöntem, üretim sürecinin hızlı ve otomatikleştirilmesine olanak tanır. Hamur, kalıp makinesindeki enjeksiyon noktasından enjekte edilir ve daha sonra kalıplara yerleştirilir. Bu yöntemle üretim hızlı ve verimlidir. Ancak, yüksek maliyetli ekipmanlar gerektirir ve üretim süreci karmaşık olabilir.
Yukarıda bahsedilen üretim yöntemlerinin her biri, seramik üretimi için benzersiz avantajlara ve dezavantajlara sahiptir. Üretim sürecinin seçimi, üreticinin üretim hedeflerine, müşteri taleplerine ve bütçesine bağlıdır.
Basınçlı Kalıplama
Basınçlı kalıplama yöntemi, seramik üretiminde en yaygın kullanılan yöntemlerden biridir. Bu yöntem, seramik malzemelerin yüksek sıcaklıkta basınç altında kalıplama işlemiyle üretilmesini sağlar. Basınçlı kalıplama yöntemi, seramiklerin yüksek mukavemetli, sert ve yüksek sıcaklık dayanımına sahip olmasını sağlar.
Bu yöntem, seramik üretiminde yüksek üretim hızı ve tekrarlanabilirliği sağlar. İstenilen sonuçları elde etmek için gerekli formülasyon ayarlamaları yapıldıktan sonra, basınçlı kalıplama yöntemiyle birçok parça aynı anda üretilebilir. Bu da süreç verimliliğini artırır ve maliyetleri düşürür.
Avantajlar | Dezavantajlar |
---|---|
|
|
Basınçlı kalıplama yöntemi, yerli ve yabancı birçok seramik endüstrisi için temel bir üretim yöntemidir. Bu yöntemin avantajları ve dezavantajları dikkate alınarak, işlemlerin düzenlenmesi, süreç kontrolü ve malzeme formülasyonları iyileştirilebilir. Ancak, bu yöntemle üretilen seramiklerin kalitesi ve mukavemeti genellikle daha yüksektir.
Sınır Alanı Yöntemi
Sınır alanı yöntemi seramik üretimi için kullanılan bir yöntemdir. Bu yöntem, seramik hammaddesinin toz halinde olduğu sıvı bir karışıma dönüştürülmesini içerir. Sınır alanındaki sıvılaşma, farklı malzemelerin bir arada kullanılmasına imkan tanır ve sonuç olarak daha dayanıklı ve etkileyici seramikler üretilir.
Bu yöntemin avantajlarından biri, diğer seramik üretim yöntemlerine göre daha düşük sıcaklıklarda çalışabilmesidir. Bu, enerji tasarrufu sağlar ve üretim maliyetini azaltır. Ayrıca, sınır alanı yöntemi ile üretilen seramikler yüksek yoğunluklu ve daha homojen bir yapıya sahiptirler. Bu da, seramiklerin daha yüksek mukavemetli ve daha az çatlama eğilimli olmasını sağlar.
Sınır alanı yöntemi ayrıca, diğer üretim yöntemlerine kıyasla daha fazla malzeme çeşitliliği sağlar ve farklı malzemelerin bir arada kullanılabilmesine olanak tanır. Bu, seramik üreticilerinin daha özgün ve yaratıcı tasarımlar oluşturmasına yardımcı olur.
Sınır alanı yöntemi ile üretilen seramikler, dayanıklılık, yüksek sıcaklık dayanımı ve kimyasal direnç gibi özellikleri nedeniyle endüstriyel uygulamalarda sıkça kullanılır. Ayrıca, bu yöntemle üretilen seramikler, çeşitli ev dekorasyonu ürünleri gibi tüketici ürünleri için de kullanılabilir.
Enjeksiyon Kalıplama
Enjeksiyon kalıplama, seramiklerin üretiminde sıklıkla kullanılan bir yöntemdir. Bu yöntem, yüksek basınç altında seramik malzemesinin kalıba enjekte edilmesiyle gerçekleştirilir. Enjeksiyon kalıplama, diğer yöntemlerle kıyaslandığında daha hızlı bir şekilde çalışır ve istenilen şekil ve boyutlarda seramik parçaları üretmek için çok yönlüdür.
Enjeksiyon kalıplama yönteminin avantajları arasında, malzeme atığından tasarruf edilmesi, yüksek verimlilik, tekrarlanabilirlik ve düşük maliyet bulunur. Bu yöntem aynı zamanda daha ince ve karmaşık parçaların üretilmesine de olanak tanır.
Bu yöntem, seramik üretiminde sıklıkla kullanılan bir yöntem olmasına rağmen, bazı dezavantajları da vardır. Özellikle, bu yöntemle üretilen seramikler genellikle daha düşük yoğunluğa sahiptir, bu da malzemenin dayanıklılığını azaltabilir. Bu nedenle, belirli uygulamalar için en uygun seramik üretim yöntemi seçilmelidir.
Enjeksiyon kalıplama yöntemi, seramik endüstrisindeki birçok uygulamada kullanılır. Bu uygulamalar arasında, diş implantları, izolatörler, yüksek basınçlı aletler ve hassas elektronik bileşenler yer alır.
Seramik Üretimindeki Temel İlkeler
Seramik üretiminin temel ilkeleri, seramik bileşenlerinin özelliklerine, üretim işlemi sırasındaki malzeme hazırlığına ve ısıtma yöntemlerine bağlıdır. Üretim sürecinde kullanılacak malzemelerin doğru oranlarda karıştırılması gibi basit adımlar önemli bir rol oynar. Malzemelerin doğru oranlarda karıştırılması, seramiklerin nihai özelliklerindeki farklılıkları belirler.
Seramiklerin üretiminde kullanılan bazı temel ilkeler arasında malzeme hazırlığı, şekil verme ve ısıtma süreçleri yer alır. Bileşenlerin stabilizasyonu, yapışma ve sinterleme adımları seramik üretiminde çok önemlidir. Malzeme hazırlığı, kumlu ve tozlu hammaddelerin öğütülmesini, birlikte karıştırılmasını ve bazen önceden fırınlanmalarını içerir. Bu süreç, yapılacak seramik türüne ve uygulanan yönteme bağlı olarak değişiklik gösterir.
Şekillendirme adımları seramik üretimi sürecindeki en önemli adımlardan biridir. Bu aşamada çimento sıvı hale getirildiğinde kalıplar, hava kilçi, bantı ve presler kullanılır. Isıtma süreci iki ana aşamada gerçekleştirilir – sinterleme ve fırın etkisi. Sinterleme, malzemelerin yüksek sıcaklıklara maruz kalması sonucu püskürtme kristallerinin formuna dönüştürülmesidir. Buna karşılık, fırın etkisi, bir malzemenin yumuşaklığını artırmak için düşük sıcaklıklarda termal işlem görmesi işlemidir.
Seramik üretimi, çeşitli teknikleri kullanarak yapılabilir. Bunlar arasında basınçlı kalıplama, sınır alanı yönteminde, seramik tozları sıkıştırılır; enjeksiyon kalıplama ise, seramik parçalar enjeksiyon kalıpları kullanılarak üretilir.
Sonuç olarak, seramik üretimi samimi olarak bilgi, deneyim ve yaratıcılık gerektiren bir süreçtir. Her üretimin tekniği ve uygulandığı malzemeler farklıdır. Ancak seramik üretiminin temel ilkeleri her zaman geçerlidir, doğru izlenirse ürünlerin mükemmel olması için büyük bir etkisi olacaktır.
Kimya ve Seramik Endüstrisindeki Kariyer Olanakları
Kimya ve seramik endüstrisi, yaratıcılık, yenilik ve teknolojik gelişimi destekleyen bir endüstridir. Bu endüstride birçok farklı kariyer seçeneği bulunmaktadır. Kimya endüstrisinde çalışmak, kimyasal maddelerin keşfi, geliştirilmesi ve uygulanmasını içerir. Seramik endüstrisi ise, seramik hammaddelerin işlenmesi, biçimlendirilmesi ve işlenmesiyle ilgilidir.
Bu endüstrilerde çalışmak için, mühendislik, kimya, malzeme bilimi, iş yönetimi, pazarlama, satış veya finans alanlarında eğitim almış olmak gerekebilir. Kimya ve seramik endüstrisinde, araştırmacılar, mühendisler, tasarımcılar, teknisyenler, proje yöneticileri, yöneticiler, pazarlama uzmanları ve satış temsilcileri gibi çok sayıda farklı pozisyonlar bulunmaktadır.
Bunun yanı sıra, var olan bilgilere dayalı, malzeme karakterizasyonu, kalite kontrolü, üretim planlama, üretim makinelerinin bakımı, tedarik zinciri yönetimi, insan kaynakları, AR-GE gibi pozisyonlar da mevcuttur. Kimya ve seramik endüstrisi ayrıca, hem yerel hem de küresel olarak çalışma olanağı, işletmelerin çeşitli seviyelerinde çalışma olanağı, iş garantisi ve potansiyel bir yüksek gelir sağlama gibi fırsatlar sunar.
Aşağıda, kimya ve seramik endüstrisindeki kariyer seçeneklerinden bazıları verilmiştir:
Pozisyonlar | Görevleri |
---|---|
Kimya Mühendisi | Kimyasal reaksiyonları geliştirme, ürün tasarımı, kalite kontrolü ve üretim süreçlerinin yönetimi |
Malzeme Bilimcisi | Malzemelerin fiziksel ve kimyasal özelliklerini inceler, malzemelerin tasarımı ve geliştirilmesi konusunda çalışır |
Satış ve Pazarlama Uzmanı | Ürünlerin pazarlanması, müşterilerle etkileşim kurulması, satış stratejilerinin geliştirilmesi ve müşteri memnuniyetinin sağlanması |
Proje Yöneticisi | Proje planlama, yönetim ve kontrolü, proje bütçesi ve programı çerçevesinde proje sürecinin yönetilmesi |
Üretim Yöneticisi | Üretim süreçlerinin planlanması, yönetimi ve kontrolü, üretim taşıyıcı sistemlerin yönetimi, iş güvenliği ve kalite kontrolü |
Bunlar sadece birkaç örnektir. Kimya ve seramik endüstrisinde birçok farklı kariyer seçeneği mevcuttur. Kendi yeteneklerinizi, ilgi alanlarınızı ve deneyimlerinizi düşünerek hangi pozisyonların size uygun olabileceğine karar verebilirsiniz.