Makine elemanları, mühendisler tarafından tasarlanan parçaların birleştirilmesiyle oluşur Mekanik montaj teknikleri, doğru birleştirme işlemi için en önemli adımdır Bu yazıda, vidalama ve kaynak yöntemleri anlatılmaktadır Vida ve somun montajının doğru seçim, hazırlık ve kontrolünün yapılması önemlidir Kaynak yöntemleri de metal parçaların birleştirilmesinde kullanılır Gazaltı kaynağı, TIG kaynağı, MIG/MAG kaynağı ve elektron ışın kaynağı gibi farklı yöntemler vardır Her biri farklı amaçlar için kullanılır ve avantajları ve dezavantajları vardır
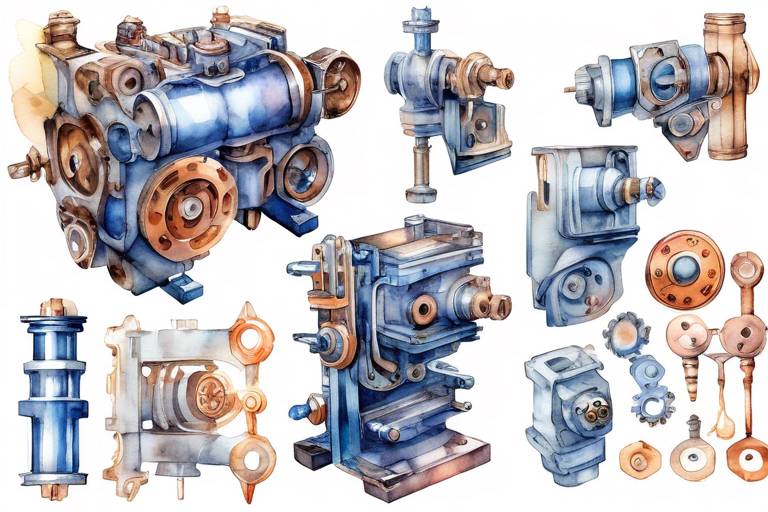
Makine elemanları, mühendisler tarafından tasarlanan parçaların birleştirilmesiyle oluşur. Bu parçaların doğru şekilde birleştirilmesi, makinenin performansını ve ömrünü etkiler. Mekanik montaj teknikleri, bu birleştirme işleminin en önemli adımlarından biridir.
Bu makalede, mekanik montaj tekniklerinin çeşitleri ve örnekleri anlatılacak. Yapısına göre farklılık gösteren montaj yöntemleri, doğru uygulandığında makinelerin daha uzun ömürlü ve performanslı olmasına büyük katkı sağlarlar.
Vida ve Somun Montajı
Vida ve somun montajı, birçok mekanik sistemde en sık kullanılan birleştirme yöntemidir. Doğru vida ve somun seçimi, montaj öncesi hazırlıklar ve montaj sonrası kontrol, bu yöntemin doğru bir şekilde uygulanmasını sağlayabilir.
İlk olarak, doğru vida ve somun seçimi önemlidir. Yanlış seçim, sistemdeki zayıf bir bağlantı noktasına neden olabilir ve hatta makinenin hasar görmesine de sebep olabilir. Bu nedenle, doğru boyuttaki ve kalitedeki vidalar ve somunlar seçilmelidir.
Montaj öncesi hazırlıklar, vidaların ve somunların doğru bir şekilde yerleştirilmesini sağlar. Önceden doğru yerleşim planı yapılması ve vidalar ve somunlar için uygun aralıkların bırakılması önemlidir. Ayrıca, vidaların ve somunların diş hatlarına ve yüzeylerine dikkatlice bakılması ve gerekli durumlarda yağlama işlemi yapılması gerekmektedir.
Montaj sonrası kontrol, birleşim noktasının doğru bir şekilde kurulduğundan emin olmak için yapılmalıdır. Vida ve somunların sıkıca bağlandığından ve bağlantının sallanmadığından emin olunmalıdır. Ayrıca, makinenin çalışması sırasında bağlantının gevşeme riskini en aza indirmek için düzenli kontrol işlemleri yapılmalıdır.
Kaynak Yöntemleri
Kaynak yöntemi, metal parçaların birleştirilmesinde en yaygın kullanılan yöntemdir. Bu yöntem sayesinde güçlü ve dayanıklı makineler üretmek mümkündür. Kaynak yöntemleri farklı amaçlar için kullanılır ve her birinin kendi avantajları ve dezavantajları vardır. Bunun yanı sıra, uygulandığı malzemeye göre de farklılık gösterir. Gazaltı kaynağı, TIG kaynağı, MIG/MAG kaynağı ve elektron ışın kaynağı gibi farklı kaynak yöntemleri vardır. Her biri farklı uygulamalar için kullanılır.
Gazaltı kaynağı, metal parçaların birleştirilmesi için sıklıkla kullanılan bir yöntemdir. Bu yöntemde, işlem sırasında bir gaz kullanılır. TIG kaynağı, yüksek hassasiyet gerektiren uygulamalarda tercih edilen bir yöntemdir. Bu yöntem, yüksek kaliteli kaynaklar elde etmek için kullanılır. MIG/MAG kaynağı hızlı ve verimli bir kaynak yöntemi olarak bilinir ve elektron ışın kaynağı yüksek hassasiyet ve hızlı kaynak uygulamalarında kullanılır.
Gazaltı Kaynağı
Gazaltı kaynağı, metal parçaların birleştirilmesinde kullanılan bir kaynak yöntemidir. Bu yöntem, özellikle yüksek mukavemetli ve dayanıklı kaynaklar gerektiren uygulamalarda tercih edilir. Gazaltı kaynağında, kaynak edilecek parçalar arasına bir gaz akışı sağlanarak kaynak yapılmaktadır.
Gazaltı kaynağı prosedürü, öncelikle kaynak edilecek parçaların temizlenmesiyle başlar. Daha sonra, kaynak parametreleri belirlenerek kaynak yapılacak bölgeye gaz akışı sağlanır. Kaynak yapılan parçaların birbirine tam olarak uyumlu olması, gaz akışının düzgün bir şekilde sağlanması ve kaynak hızının doğru bir şekilde ayarlanması, gazaltı kaynağının başarısı için önemlidir.
Gazaltı kaynağı, endüstriyel sektörde birçok alanda kullanılmaktadır. Özellikle otomotiv, havacılık, denizcilik gibi sektörlerin yanı sıra, inşaat ve savunma sanayi gibi birçok alanda da gazaltı kaynağı yöntemi tercih edilmektedir.
TIG Kaynağı
TIG kaynağı, Tungsten İnert Gaz (TIG) adı verilen bir tekniği kullanarak yapılan bir kaynak yöntemidir. Yüksek hassasiyet gerektiren uygulamalarda parçaların birleştirilmesi için tercih edilir. TIG kaynağı, mükemmel bir görünüme ve yüksek hassasiyete sahip kaynaklar oluşturur. Bu nedenle otomotiv sektöründe, tıp sektöründe, havacılık sektöründe ve hassas cihaz üretiminde sıklıkla kullanılır.
TIG kaynağı, kaynak işlemi sırasında bir elektrot (genellikle tungsten) kullanır. Yüksek oranda saf bir gaz (genellikle argon) kullanılarak, havanın oksijen içeriği ortadan kaldırılır ve böylece kaynak bölgesinde oksit oluşumuna engel olunur. Bu, kaynak bölgesinin daha temiz ve daha düzgün bir görünüm kazanmasına yardımcı olur. TIG kaynağı işlemi sırasında, kaynak bölgesi soğumasını önlemek için su soğutmalı tüpler kullanılmalıdır.
TIG Kaynağı Avantajları | TIG Kaynağı Dezavantajları |
---|---|
- Yüksek hassasiyet ve mükemmel bir görünüm sağlar. | - Diğer kaynak yöntemlerine göre daha yavaş bir kaynak işlemidir. |
- Daha az atık ve çevre dostudur. | - Daha yüksek maliyetli bir kaynak yöntemidir. |
- Çok sayıda malzeme ile uyumludur. | - Eski ve korozyonlu metal parçaları kaynağı için uygun değildir. |
TIG kaynağı, genellikle ince parçaların birleştirilmesi için kullanılır. Örneğin, tıp sektöründe, hassas cihazların üretiminde TIG kaynağı sıklıkla kullanılır. Bununla birlikte, diğer kaynak yöntemleri gibi, TIG kaynağı da belli bir öğrenme eğrisi gerektirir ve ayrıca daha yüksek maliyetlidir.
MIG/MAG Kaynağı
MIG/MAG kaynak yöntemi, hızlı ve verimli bir kaynak yöntemi olarak kullanılır. Bu yöntem, metal parçaların birleştirilmesinde yaygın olarak kullanılır. MIG/MAG kaynağı, doğru ekipman kullanımı ve işlem sürecine uygun malzeme seçimi ile birlikte, güçlü ve dayanıklı kaynaklar elde edilmesini sağlar.
MIG kaynağı, ince malzemelerin birleştirilmesinde etkilidir ve genellikle alüminyum ve bakır alaşımların kaynağında kullanılır. MAG kaynağı ise, daha kalın malzemelerin birleştirilmesinde etkilidir ve genellikle çelik ve bazı alaşımların kaynağı için kullanılır.
MIG/MAG kaynağı prosedürü, kaynak öncesi hazırlık, kaynak sırasında malzeme besleme hızı, sıcaklık kontrolleri ve kaynak sonrası kontrol adımlarını içerir. Bu yöntem, doğru şekilde uygulandığında güçlü ve dayanıklı kaynaklar sağlar ve maliyeti düşürür.
Elektron Işın Kaynağı
Elektron ışın kaynağı, yüksek hassasiyet ve yüksek hızlı kaynak uygulamalarında kullanılan bir yöntemdir. Elektron ışın kaynağı, elektromanyetik bir alan içinde yüksek enerjili elektronların kullanıldığı bir kaynak yöntemidir. Bu elektronlar, elektromanyetik bir bobin kullanılarak hızlandırılır ve iş parçasına odaklanmış bir ışın oluşturmak için bir fokal noktaya odaklanır.
Elektron ışın kaynağı prosedüründe, iş parçası önceden hazırlanarak, kaynak bölgesi temizlenmeli ve işlem öncesi bir vakum oluşturulmalıdır. Ayrıca, iş parçası pozisyonu ve kaynak kafası konumu önemlidir. Elektron ışın kaynağı, ince yapılı veya küçük parçaların kaynağı için uygundur. Kaynak sırasında eriyen metal, vakum altında tutulur ve korunur. Elektron ışın kaynağı, yüksek sıcaklıklar nedeniyle bazı malzemelerde, özellikle plastiklerde, uygulanamaz. Ancak, diğer malzemeler için çok iyi bir kaynak yöntemidir.
Elektron ışın kaynağı, uzay teknolojisi, havacılık, medikal cihazlar ve diğer hassas uygulamalar gibi endüstriyel alanlarda kullanılır. Elektron ışın kaynağı, yüksek hassasiyet ve tekrarlanabilirlik gerektiren uygulamalarda çok önemlidir.
Yapıştırma ve Baskı Yöntemleri
Yapıştırma ve baskı yöntemleri, mekanik montaj teknikleri arasında alternatif bir yöntemdir. Bu yöntemler, farklı malzemelerin birleştirilmesinde kullanılabilmektedir. Yapıştırma yöntemi, yapıştırıcının kullanımına dayanırken, baskı yöntemi ise malzemelerin birbirine sıkıca bastırılması esasına dayanır.
Farklı yapıştırma yöntemleri arasında epoksi yapıştırıcısı, silikon yapıştırıcı ve poliüretan yapıştırıcı gibi çeşitler bulunur. Özellikle poliüretan yapıştırıcılar, dayanıklılığı ve çeşitli malzemelerin birleştirilmesine olanak sağlaması nedeniyle oldukça yaygın kullanılır.
Baskı yöntemleri arasında ise eklemeli baskı, hidrolik baskı ve vakumlu baskı gibi çeşitler mevcuttur. Özellikle vakumlu baskı, malzeme birleştirme işleminde yüksek hassasiyet ve kalite sağlayarak yaygın olarak kullanılmaktadır.
Birleştirilecek malzemelere göre uygun yapıştırma ve baskı yöntemlerinin seçilmesi, makine elemanlarının performansını ve dayanıklılığını arttırır. Doğru seçilmiş bir yapıştırma veya baskı yöntemi, yapıştırılan veya birleştirilen malzemelerde kalıcı bir bağlantı sağlar.
Kauçuklu Süspansiyon Mafsalları
Kauçuklu süspansiyon mafsalları, genellikle araçların süspansiyon sistemlerinde kullanılır ve şaftların hareketlerini absorbe etmeleri için tasarlanmışlardır. Bu mafsallar, yüksek titreşim ve darbe koşullarında çalışabilen dayanıklı bir yapıya sahiptirler. Üretim süreci, kaliteli bir kauçuk malzeme kullanımını içerir. Bu malzeme doğru şekilde hazırlanır ve kalıplanır. Ardından, mafsalların birleştirilmesi için özel bir bağlantı elemanı kullanılır.
Mafsalların montajı, çoğu zaman araçların bakım ve onarımı sırasında gerçekleştirilir. Bu işlem için, gerekli araçlar ve ekipmanlar kullanılmalıdır. Mafsalların doğru şekilde monte edilmesi, sürüş güvenliği ve araç performansı açısından son derece önemlidir. Montaj aşamasında, mafsalların uygun pozisyonda tutulması ve çevresel koşullara karşı dayanıklı hale getirilmesi için özellikle dikkat edilmelidir.
- Kauçuklu süspansiyon mafsallarının üretimi:
- Kauçuk malzemenin hazırlanması ve kalıplanması
- Birleştirme için özel bağlantı elemanlarının kullanımı
- Kauçuklu süspansiyon mafsallarının montajı:
- Doğru araçlar ve ekipmanların kullanımı
- Mafsalların uygun pozisyonda tutulması
- Çevresel koşullara karşı dayanıklı hale getirme
O-Ring ve Conta Uygulamaları
O-ring ve conta, sızdırmazlık uygulamalarında önemli bir rol oynar. O-ring, halka şeklinde bir contadır ve genellikle silindirik bir yüzeyde kullanılır. Conta ise düz yüzeylerde kullanılır ve O-ring gibi hemen hemen her malzemeden yapılabilir. O-ring ve conta, sıvı ve gazların geçmesini önlemek için kullanılır.
O-ring ve conta tipleri, malzeme özelliklerine göre değişir. Bunlar arasında nitril, silikon, viton, neopren ve EPDM gibi malzemeler yer alır. Her malzeme, özel koşullarda daha uygun olabilir. Örneğin, sıcaklığa veya kimyasal maddelere dayanıklı bir conta, uygun uygulama için seçilmelidir.
Bazı O-ring ve conta tipleri, kullanımlarına göre de farklılık gösterir. Örneğin, piston contaları, silindir etrafında hareket eden sürtünme ve aşınmalara dayanmak zorunda oldukları için özel olarak tasarlanmıştır. Yüksek sıcaklıklarda kullanılmak üzere sızdırmazlık bileşikleri, sıcaklık toleransı daha düşük olan malzemelerden daha dayanıklıdır.
O-ring ve conta aynı zamanda farklı ebatlarda ve şekillerde de üretilebilir. Genellikle, özel bir uygulama için uygun boyutlarda ve şekillerde seçilmelidirler. Yeterli sızdırmazlık sağlanması için uygun bir montaj tekniği de önemlidir.