Mekanik tasarımda hatalar kaçınılmazdır Bu hataların tespiti ve çözümü tasarımın güvenli ve verimli çalışmasını sağlar Tasarım hatalarının tespiti için çeşitli test ve analiz yöntemleri kullanılır Prototip üretiminde ise deneyimsel metot, malzeme analizi, simülasyon ve gözlemcilerin raporları gibi teknikler kullanılır Doğrulama testleri ise kullanılabilirlik, yapısal güvenlik, akışkan simülasyon, titreşim ve sıcaklık testlerini içerir Hataların giderilmesi ise tasarım yenileme, parça ve malzeme seçimi gibi tekniklerle yapılır Bakım ve onarım da önemlidir
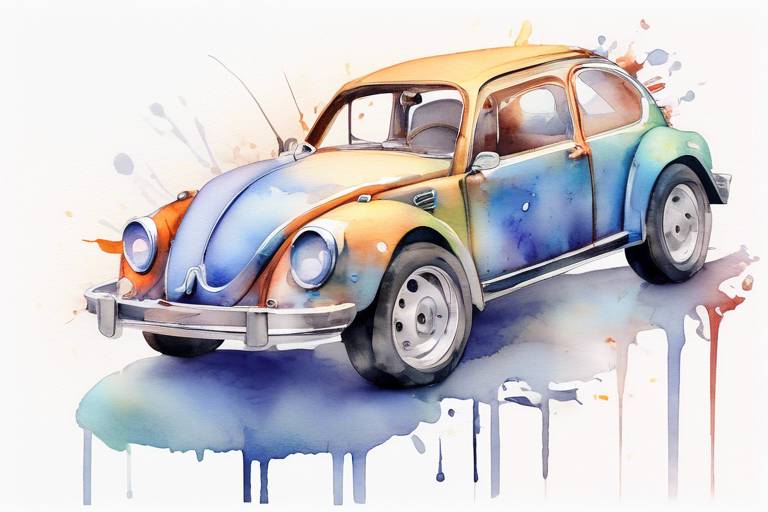
Mekanik tasarımların oluşturulma sürecinde hatalar kaçınılmazdır. Bu hataların tespit edilmesi ve çözümlenmesi, tasarımın güvenli ve verimli çalışmasını sağlar. Tasarım hatalarının tespiti için çeşitli test ve analiz yöntemleri kullanılabilir. Prototip üretim aşamasında da tasarım hatalarının tespit edilmesi önemlidir. Bu aşamada kullanılan teknikler, tasarımın hatalarının çözülmesine yardımcı olur.
Tasarım hataları tespit edildikten sonra, doğru çözüm tekniklerinin kullanılması hataların giderilmesine yardımcı olacaktır. Tasarım yenileme, parça ve malzeme seçimi gibi teknikler, tasarım hatalarının giderilmesine yardımcı olur. Bakım ve onarım da mekanik tasarımların güvenli ve verimli çalışması için önemlidir.
Tasarım Hatalarının Tespiti
Tasarım hatalarının tespiti için çeşitli test ve analiz yöntemleri kullanılabilir. Örneğin, stres testleri tekniği ile tasarımda oluşabilecek mukavemet problemleri tespit edilebilir. Buna ek olarak, titreşim ve akışkan analizi yöntemleri de tasarım hatalarının tespiti için yaygın olarak kullanılmaktadır.
- Stres testleri: Bu yöntemde, tasarımın öngörülen yük altında nasıl davrandığı test edilir. Bu yükler genellikle tasarımın maksimum kapasitesine yakın yüklerdir.
- Titreşim analizi: Tasarımlar çoğu zaman titreşimlere maruz kalır. Titreşim analizi yöntemiyle tasarımın titreşimler sırasında nasıl davrandığı ve titreşimlerin yapıya zarar verip vermediği tespit edilebilir.
- Akışkan analizi: Akışkanlarla çalışan tasarımlarda akışkan analizi yöntemi kullanılır. Bu yöntemde, akışkanın nasıl davrandığı ve tasarımda hangi hataların bulunduğu tespit edilir.
Bunlar sadece birkaç örnektir ve tasarım hatalarını tespit etmek için kullanılabilecek pek çok test ve analiz yöntemi vardır. Doğru testler ve analizler ile tasarım hatalarının tespiti kolaylaştırılabilir ve daha güvenilir bir mekanik tasarım ortaya çıkabilir.
Prototip Üretiminde Hata Ayıklama
Prototip üretimi sırasında hata ayıklama, tasarım hatalarının tespit edilip düzeltilmesi açısından oldukça önemlidir. Bunun için farklı teknikler ve metotlar kullanılmaktadır. Bunlar arasında en sık kullanılanlar şunlardır:
- Deneyimsel Metot: Bu yöntemde, prototipin özellikleri ve performansı, deneyimli bir tasarımcı tarafından gözlem ve deneyim yoluyla analiz edilir. Tasarımcının deneyimleri sayesinde olası hatalar ve sorunlar tespit edilebilir.
- Malzeme Analizi: Prototipte kullanılan malzemelerin analizi yapılır ve bu malzemelerin özellikleri incelenir. Malzeme özelliklerindeki anormallikler veya hatalar bu sayede tespit edilir.
- Simülasyon: Prototipin simülasyonu yapılır ve tasarım hataları bu sayede tespit edilir. Simülasyonlarda tasarımın gerçek ortamda nasıl çalışacağı simüle edilir ve olası hatalar belirlenir.
- Gözlemcilerin Raporları: Prototipin test edildiği ortamda gözlemciler tarafından hazırlanan raporlar, prototipteki hataların tespiti açısından oldukça önemlidir.
Doğrulama Testleri
Doğrulama testleri, tasarım hatalarını tespit etmek için sıklıkla kullanılan testlerdir. Bu testler tasarımın özelliklerinin doğrulanması, performansın kontrol edilmesi ve tasarımın beklenen işlevlerini yerine getirip getirmediğinin belirlenmesi amacıyla yapılır. Tasarım hatalarını tespit etmek için kullanılan doğrulama testleri arasında kullanılabilirlik testleri, yapısal güvenlik testleri, akışkan simülasyon testleri, titreşim testleri ve sıcaklık testleri sayılabilir. Doğrulama testleri, mühendislerin ve tasarımcıların tasarımın doğruluğunu doğrulamalarına yardımcı olur, böylece müşterilere güvenilir bir ürün sunulabilir.
Doğrulama testleri, tasarım sürecinin farklı evrelerinde yapılabilir. Tasarımın erken evrelerinde yapılan testler, tasarımın daha az maliyetli şekilde güncellenmesine yardımcı olabilir. Bununla birlikte son evrelerde yapılan testler, tasarımın daha az değiştirilebilir olmasına rağmen daha güvenilir bir sonuç sağlayabilir. Doğrulama testleri, ürünün güvenilirliğini artırmak için özellikle önemlidir ve tasarım sürecinin ayrılmaz bir parçasıdır.
- Kullanılabilirlik Testleri: Kullanılabilirlik testleri, kullanıcıların ürünü ne kadar iyi anladıkları ve kullanabildikleri konusunda veri toplamak için kullanılır. Bu testler, kullanışlıkları ve genel kullanıcı deneyimi ile ilgili geri bildirimler sağlar.
- Yapısal Güvenlik Testleri: Tasarım hatalarının kaynaklandığı bir diğer alan olan yapısal güvenlik testleri, bir ürünün güvenliğini anlamak için kullanılır. Bu testlerde, ürünün güvenliği açısından kritik olan bileşenlerin dayanıklılığı test edilir.
- Akışkan Simülasyon Testleri: Akışkan simülasyon testleri, tasarım hatalarını tespit etmek için akışkan sistemlerde kullanılır. Bu testlerde, ürünün akışkan sistemi genellikle bilgisayar yazılımı kullanılarak modellenir ve test edilir.
- Titreşim Testleri: Titreşim testleri, ürünlerin titreşim ve şok süreçlerinde performansının incelenmesine yardımcı olur. Bu testler, ürünün titreşim ve şoklara dayanıklılığını değerlendirmek için gerçekleştirilir.
- Sıcaklık Testleri: Sıcaklık testleri, tasarım hatalarını tespit etmek için ürünlerin sıcaklık aralıklarında test edilmesini sağlar. Bu testler, sıcaklık dalgalanmalarının ürünün performansına, dayanıklılığına ve ömrüne nasıl etki ettiğini inceleyerek ürünün sıcaklık döngüleri sırasında nasıl çalışacağına dair bilgi toplar.
Konsept Doğrulama Testleri
Konsept doğrulama testleri, mekanik tasarımın önceden belirlenmiş özelliklerini test etmek ve tasarımın zayıf noktalarını tespit etmek için kullanılır. Bu testler, tasarımın taslak ve kavram aşamasında gerçekleştirilir. Amaç, tasarımın uygulanabilirliğini ve yapılabilirliğini test etmektir.
Konsept doğrulama testleri, tasarımın özelliklerini ve özelliklerin kararlılığını test etmek için kullanılır. Bu testler ayrıca tasarımın işlevsel olduğunu ve özellikle kullanıcı ihtiyaçlarına uygun olduğunu doğrulamak için de yapılır. Konsept doğrulama testleri genellikle belirli bir prototip geliştirmeden önce yapılır.
Bunun yanı sıra, konsept doğrulama testleri, tasarımda mevcut olan potansiyel hataları ve zayıf noktaları tespit etmek için de kullanılır. Bu sayede, mevcut sorunların giderilmesi ve daha iyi bir tasarım oluşturulması için fikirler ortaya çıkar.
- Konsept doğrulama testleri kullanarak tasarımın uygulanabilirliği ve yapılabilirliği test edilir.
- Tasarımın özellikleri ve kararlılığı test edilir.
- Testler, tasarımın işlevsel olduğunu ve kullanıcı ihtiyaçlarına uygun olduğunu doğrular.
- Testlerle mevcut sorunlar tespit edilerek daha iyi bir tasarım oluşturulması sağlanır.
Performans Testleri
Performans testleri, mekanik tasarımların anahtar özelliklerinin kontrol edilmesi ve tasarım hatalarının tespit edilmesinde oldukça önemlidir. Bu testler, tasarımın doğru çalışması, verimliliği ve güvenliği için gereklidir. Performans testleri, ürünün gerçek kullanım koşullarına benzer koşullar altında yapılır ve ürünün performansını ölçer.
Bu testler sırasında, tasarımın belirli özellikleri test edilir. Örneğin, bir aracın hızlanma ve frenleme performansı, bir makinenin verimliliği veya bir ürünün güvenlik özellikleri gibi. Test sonuçlarına göre, tasarımın iyileştirilmesi veya eksikliklerin giderilmesi gerekebilir.
Performans testleri, farklı test cihazları veya yazılımlar kullanılarak yapılabilir. Bu testler genellikle, bazı standartlara ve yönergelerin belirlenmiş olduğu test prosedürleri ile yapılır. Böylece, test sonuçları daha objektif ve doğru olur.
Simülasyon
Mekanik tasarım hatalarının ayıklanmasında simülasyonlar oldukça kullanışlıdır. Simülasyon, gerçek dünya koşullarını taklit etmek için geliştirilmiş bir yöntemdir. Simülasyon programları, tasarımın gerçekleşmesi için gereken malzemeleri, işlevleri ve belirli sınırlara dayanan faktörleri modüle ederler.
Bu şekilde, tasarımın bir prototip olmadan bile gerçekleşmesi mümkündür. Mevcut simülasyon teknolojileri sayesinde, mekanik tasarımların simülasyonu oldukça kolaylaşmıştır. Örneğin, bilgisayar destekli tasarım (CAD) yazılımı, sanal bir prototip oluşturma sürecinde simülasyon için kullanılabilir.
Bir diğer avantajı ise, simülasyonların tekrarlanabilir, tutarlı ve kesin sonuçlar sağlamasıdır. Bu, tasarım hatalarının teşhis edilmesini ve düzeltilmesini kolaylaştırır. Özellikle, tasarımın işletim koşulları altında davranışını modüle ederek simülasyon yapmak, tasarım hatalarının önemli bir çoğunluğunu tespit etmek için kullanılır.
Tasarım simülasyonları, mekanik tasarım mühendislerinin, geliştirilen tasarımın ne kadar iyi çalışacağına dair bir fikir edinmelerini sağlar. Böylece, prototipin üretimine geçmeden önce tasarımların kökenindeki problemler belirlenebilir ve düzeltilir. Çünkü prototip üretimi genellikle yüksek maliyetlidir ve uygulamada çok fazla zaman kaybına neden olabilir.
Tasarım Hatalarının Çözümü
Tasarım hataları tespit edildiğinde, doğru çözüm tekniklerinin kullanılması tasarımın performans ve güvenilirliğini arttıracaktır. Tasarım hatalarının çözümü için kullanılan başlıca teknikler tasarım yenileme, parça ve malzeme seçimi ve bakım/onarım işlemleridir. Tasarım yenileme, mevcut tasarımın iyileştirilmesine ve hatalarının giderilmesine yardımcı olur. Parça ve malzeme seçimi doğru yapıldığında tasarım hatalarının oluşması engellenebilir. Bakım ve onarım işlemleri ise tasarımın güvenli ve verimli bir şekilde çalışmasını sağlar.
Bunların yanı sıra, tasarım hatalarının çözümü için ekip çalışmasının önemi de büyüktür. Çalışmalar sırasında farklı uzmanlıklara sahip kişilerin bir araya gelerek tasarımdaki hataların tespiti ve çözümü için işbirliği yapmaları gerekmektedir. İletişim, planlama ve uygulama sürecinin doğru bir şekilde yönetilmesi tasarım hatalarının etkisini minimize edecek ve tasarımın performansını arttıracaktır.
Tasarım Yenileme
Tasarım yenileme, mevcut bir tasarımın daha iyi hale getirilmesi ve hataların giderilmesine yardımcı olan bir süreçtir. Bu süreçte öncelikle tasarımın mevcut durumda ne kadar başarılı olduğu ve nelerin düzeltilmesi gerektiği belirlenir. Bu noktada tasarımın amacı, kullanım koşulları, malzeme kullanımı gibi faktörler göz önünde bulundurulur.
Tasarım yenileme süreci, daha gelişmiş tasarım teknikleri, daha yüksek kaliteli malzemeler veya daha iyi üretim yöntemleri kullanarak mevcut tasarımı geliştirmeye yönelik bir yaklaşımı kapsar. Tasarım yenileme sürecinde, kullanılan parçaların bileşimi, bağlantı şekilleri gibi pek çok farklı faktör göz önünde bulundurulur.
Bunun yanı sıra, tasarım yenileme süreci, önceki tasarımın eksikliklerinin ve hatalarının giderilmesini de içerir. Bu amaçla, tasarım yenileme sürecinde doğru analiz yöntemleri kullanılmalı ve hata ayıklama süreci tamamlanmalıdır. Ayrıca, yeni tasarımın performansı ölçülmeli ve karşılaştırılmalıdır.
Tasarım yenileme sürecinde, mevcut olan tasarımın daha iyi bir hale getirilmesine yönelik pek çok farklı yöntem kullanılabilir. Örneğin, reverse engineering yöntemi kullanılarak mevcut tasarımın farklı bir açıdan ele alınması mümkündür. Ya da malzeme ve parça seçiminde yapılacak değişiklikler ile tasarım daha iyi hale getirilebilir. Bunlar gibi birçok farklı yöntem, tasarım yenileme sürecinde kullanılabilecek seçeneklerden sadece birkaçıdır.
Tasarım yenileme süreci oldukça önemlidir, ancak dikkatli bir şekilde planlanmalıdır. Herhangi bir tasarım yenileme işlemi öncesinde detaylı bir analiz yapılmalı ve olası riskler göz önünde bulundurulmalıdır. Ayrıca, tasarım yenileme sürecinde de doğru test ve analiz yöntemleri kullanılmalıdır.
Parça ve Malzeme Seçimi
Tasarımda doğru parça ve malzeme seçimi, tasarımın kalitesi ve güvenliği açısından son derece önemlidir. Yanlış seçimler, tasarım hatalarına yol açabilir ve istenmeyen sonuçlar doğurabilir. Bu nedenle, tasarımcılar seçecekleri parça ve malzemeleri dikkatlice seçmeli ve seçimlerinin tasarımın gereksinimlerini karşıladığından emin olmalıdırlar.
Malzeme seçimi özellikle önemlidir, çünkü yanlış malzeme seçimi, tasarımın dayanıklılığı, ağırlığı ve maliyeti üzerinde doğrudan etkisi bulunabilir. Tasarımcılar, malzeme seçiminde tasarım parametrelerini, kullanım koşullarını ve üretim maliyetlerini dikkate almalıdırlar.
Parça seçimi de benzer şekilde dikkatli bir analiz gerektirir. Yanlış parça seçimi, tasarımın uyumluluğunu ve doğru çalışmasını etkileyebilir. Parça seçiminde, parçanın özellikleri, boyutları, uyumluluğu ve maliyetleri göz önünde bulundurulmalıdır.
Ek olarak, sıklıkla kullanılan parçaların birçok alternatifi ve malzemeleri mevcut olabilir. Tasarımcıların, her parça ve malzeme seçimi için alternatifleri araştırması ve doğru seçimi yapması önemlidir.
Özetle, tasarımda parça ve malzeme seçimi, tasarımın kalitesi ve güvenliği açısından son derece önemlidir. Doğru seçimler, tasarımın uyumluluğunu, maliyetlerini ve dayanıklılığını etkilerken yanlış seçimler, tasarım hatalarına yol açabilir. Tasarımcıların, tasarım için doğru parça ve malzeme seçimine dikkat etmesi gerekir.
Bakım ve Onarım
Mekanik tasarımlarının güvenli ve verimli çalışabilmesi için düzenli bakım ve onarım işlemleri oldukça önemlidir. Bu işlemler, mekanik parçaların ve ekipmanların ömrünü uzatırken, aynı zamanda öngörülemeyen arızaların önlenmesine yardımcı olur.
Bakım ve onarım işlemleri genellikle iki farklı şekilde gerçekleşir. Birincisi, düzenli periyodik bakımlar ile yapılır. Bu bakımlar, belirli bir süreçte mekanik parçaların kontrol edilmesi, temizlenmesi ve gerekli onarımların yapılmasıdır. İkincisi ise, beklenmedik bir arıza durumunda yapılan acil onarım işlemleridir.
Bakım işlemleri sırasında aşağıdaki unsurlar dikkate alınmalıdır:
- Yağlama: Mekanik parçalar düzenli aralıklarla yağlanmalıdır. Bu işlem, aşınma ve hasarın önlenmesine yardımcı olur.
- Temizlik: Parçaların düzenli olarak temizlenmesi, özellikle toz, yağ ve kir gibi unsurların olumsuz etkisinden korunmalarını sağlar.
- Kontrol: Bakım işlemleri sırasında mekanik parçaların kontrol edilmesi ve gerekirse onarım yapılması, parçaların ömrünü uzatır ve arızaların önlenmesine yardımcı olur.
Onarım işlemleri ise genellikle beklenmedik bir arıza durumunda gerçekleşir. Bu işlemler, genellikle profesyonel bir teknisyen tarafından gerçekleştirilir. Onarımların yapılması esnasında, mekanik parçaların değiştirilebilecekleri veya tamir edilebilecekleri değerlendirilir.
Tabi ki, bakım ve onarım işlemleri sırasında öngörülmeyen durumlarla da karşılaşılabilir. Bu durumlarda, gerekli tedbirler alınarak, sorunların hızlıca çözülmeleri sağlanır.
İyi bir bakım ve onarım programı, mekanik parçaların yüksek verimle ve güvenle çalışmasını sağlar. Bu nedenle, bakım ve onarım işlemlerinin düzenli olarak yapılması, ciddi arızaların önlenmesine katkı sağlar.