Endüstriyel mühendislikte doğruluk kontrolü, üretim süreçlerinde önemli bir faktördür İstatistiksel kontrol süreçleri, kalite güvence ve kalite kontrol süreçleri, yüzde hata oranı ve Pareto analizi gibi araçlar, tasarım deneyleri bu kontrolün sağlanmasında kullanılabilir İstatistiksel kontrol süreçleri, üretim hatalarını minimum seviyeye indirmek ve ürünlerin kalitesini arttırmak için kullanılan en yaygın yöntemlerden biridir Kalite güvence sürecinde kullanılan araçlar ve teknikler ise ürün ve hizmet kalitesinin müşteri beklentilerine uygun olarak sağlanması için önemlidir Kalite kontrol ise ürün ve hizmetlerin belirlenen standartlara uygun olup olmadığının kontrol edilmesi için kullanılır
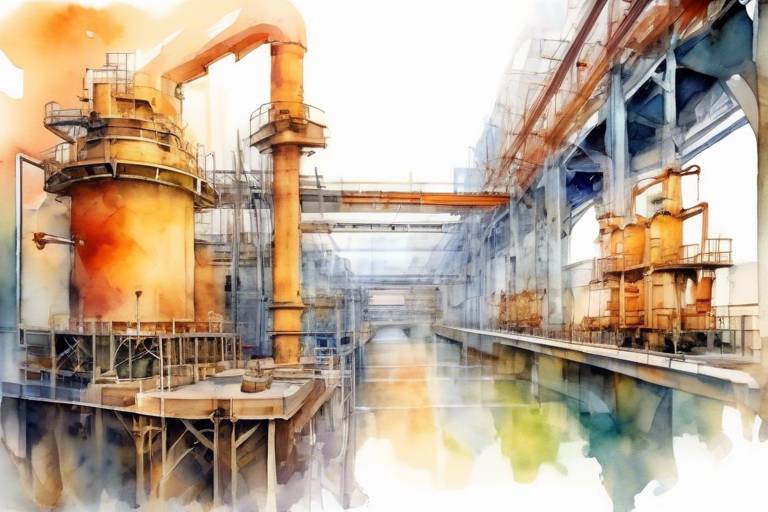
Endüstriyel mühendislikte doğruluk kontrolü, üretim süreçlerinin yönetiminde temel bir faktördür. Doğruluk kontrolü, üretim hatasını minimum seviyede tutabilmek ve ürünlerin veya hizmetlerin kalitesini arttırmak için çok önemlidir. Endüstriyel mühendislerin bu konuda kullanabileceği farklı yöntemler ve teknikler vardır.
Bunların arasında en yaygın olanı istatistiksel kontrol süreçleridir. İstatistiksel kontrol süreleri, üretim hatalarının sürekli olarak takip edilmesi ve gerekli müdahalelerin yapılması için kullanılan bir yöntemdir. Ayrıca, kalite güvence ve kalite kontrol süreçleri de doğruluk kontrolünde sıkça kullanılan diğer yöntemler arasındadır. Bu süreçler, ürünlerin veya hizmetlerin kalitesini ölçmek ve hataların tespit edilmesi için çok faydalıdır.
Kalite kontrolü altında kullanılan yüzde hata oranı ve Pareto analizi gibi araçlar, üretim süreçlerinin doğruluğunu kontrol etmek için önemlidir. Ayrıca, ilk örnek kontrolü (IPC) de üretim süreçlerinde kullanılan bir yöntemdir ve ürünlerin kalitesinin başlangıçtan itibaren kontrol edilmesini sağlar.
Tasarım deneyleri de, ürün veya hizmet tasarımı aşamasında kullanılan bir diğer doğruluk kontrol yöntemidir. Bu yöntem, tasarım süreçlerinde olası hataları tespit etmek ve gidermek için kullanılır.
Birinci Alt Başlık: İstatistiksel Kontrol Süreçleri
İstatistiksel kontrol süreçleri, endüstriyel mühendislikte yaygın olarak kullanılan bir yöntemdir. Bu yöntem, bir üretim sürecinin kontrolünü ele alır ve üretim hatalarının tespit edilmesini, azaltılmasını sağlar. İstatistiksel kontrol süreçleri, sürekli değişen üretim ortamlarında kullanılmaktadır. Bu yöntemin temel amacı, sürecin ne kadar iyi çalıştığını ölçmek ve üretim hatalarını tespit etmektedir. İstatistiksel kontrol süreçleri, uygun bir şekilde uygulandığında, kalite kontrol işleminin sonuçlarını iyileştirmek için etkili bir araçtır.
İstatistiksel kontrol süreci, bir örneklemde meydana gelen değişiklikleri takip etmek için istatistiksel yöntemler kullanır. Bu yöntem, örnekleme yapılan üretim işleminin her bir aşamasında verilerin toplanmasını ve analiz edilmesini gerektirir. Bu sayede, ürünlerin kalitesi ile ilgili veri elde edilir ve üretim hatalarının ortadan kaldırılması sağlanır. İstatistiksel kontrol süreçleri, hem aykırı değerleri hem de değişen eğilimleri izlemek için tasarlanmış istatistiksel yöntemler kullanmaktadır.
- İstatistiksel kontrol süreçleri, sürekli bir iyileştirme sürecidir ve endüstriyel mühendisliğin temelini oluşturur.
- Bu süreç, üretim hatalarını tespit etmek ve azaltmak için büyük ölçüde etkilidir.
- İstatistiksel kontrol süreçleri, ürün kalitesini artırmak ve müşteri memnuniyetini en üst düzeye çıkarmak için tasarlanmıştır.
- Endüstriyel mühendislikte, istatistiksel kontrol süreçleri yaygın bir şekilde kullanılmaktadır ve her üretim işlemi için özelleştirilebilir.
Bu nedenle, endüstriyel mühendislikte doğruluk kontrolü için istatistiksel kontrol süreçleri, en popüler yöntemlerden biridir. İstatistiksel kontrol süreçleri, hem ürün kalitesinin hem de müşteri memnuniyetinin artırılmasına yardımcı olur.
İkinci Alt Başlık: Kalite Güvence
Kalite güvence sürecinde kullanılan araçlar ve teknikler arasında belgelendirme, kalite planı hazırlama, kalite kontrol, performans ölçümü ve iyileştirmeler yer almaktadır. Kalite güvence sürecinin temel amacı, hizmet veya ürün kalitesinin müşteri ihtiyaçlarına ve beklentilerine uygun olduğunu garanti etmektir.
Kalite kontrol ise üretim sürecinde kullanılan bir araçtır ve ürünlerin kalitesinin belirli standartlarla uyumlu olduğundan emin olmak için kullanılır. Kalite güvence sürecinde kalite kontrol, süreçlere doğru şekilde uygulandığında elde edilen sonuçların tutarlılığını sağlar. Ayrıca, kalite kontrol süreci, üretim hatalarının tespit edilip iyileştirilmesi için kullanılır.
- Bir diğer kalite güvence aracı olan belgelendirme süreci, müşterilerin ürün veya hizmet kalitesine olan güvenini artırmak için kullanılır. Belgelendirme süreci, uluslararası standartlara uygun olarak gerçekleştirilir ve ürün veya hizmetin müşteri ihtiyaçlarına uygun olduğunu gösteren bir belge verilir.
- Performans ölçümü, işletmenin belirlenmiş hedeflerine ne kadar yakın olduğunu belirlemek için kullanılır. Performans ölçümü, işletmenin çalışma yöntemlerinin iyileştirilmesi için kullanılan önemli bir araçtır.
- Kalite planı hazırlama süreci, belirlenmiş kalite hedeflerine ulaşmak için kullanılır. Bu süreçte, işletmenin hedefleri ve hedeflere ulaşmak için kullanılacak stratejiler belirlenir.
- Son olarak, iyileştirme süreci, işletmenin kalite hedeflerine ulaşmasını sağlamak için kullanılır. İyileştirmeler, sürekli olarak yapılmalı ve işletmenin kalite hedeflerinin belirlenmesinden sonraki süreçte aktif şekilde uygulanmalıdır.
Yukarıda bahsedilen araçlar ve teknikler, işletmelerin kalite güvencesi sağlamak için kullanabileceği birçok farklı yöntemdir. Bu araçlar ve tekniklerin doğru bir şekilde uygulanması, ürün ve hizmet kalitesinin müşteri beklentilerine uygun olarak sağlanması için büyük bir önem taşır.
Alt Alt Başlık: Kalite Kontrol
Kalite kontrol sürecinde, ürünlerin ve hizmetlerin kalitesinin belirlenmesi ve belirlenen kalite standartlarına uygun olup olmadığının kontrol edilmesi gerekmektedir. Bu süreçte kullanılan yöntemler arasında, ürünleri veya hizmetleri denetlemek, test etmek, ölçmek ve analiz etmek yer almaktadır. Kalite kontrol sürecindeki amaç, ürün veya hizmetlerin hata oranını azaltmak ve müşteri memnuniyetini artırmaktır.
Kalite kontrol sürecinde kullanılan yöntemler arasında, toplam kalite yönetimi, sürekli iyileştirme, kontrol listeleri, istatistiksel kontrol süreçleri, kontrol grafikleri, pareto analizi ve sıfır hata hedefleri yer almaktadır. Kontrol listeleri, ürünlerin veya hizmetlerin belirli aşamalarında yapılması gereken kontrolleri listelemektedir. İstatistiksel kontrol süreçleri ise, üretim sürecindeki hataları tespit etmek ve bu hataların sebeplerini analiz etmek için kullanılan bir yöntemdir.
Kalite kontrol sürecinde, önemli bir gösterge olan yüzde hata oranı, her üründe veya hizmette belirlenen standartlara uygun olarak yapılan kontrollerin sayısını hatalı olanların sayısına bölünmesi ile hesaplanmaktadır. Pareto analizi ise, endüstriyel mühendislikte hataların yüzde oranını belirlemek için kullanılan bir yöntemdir. Sıfır hata hedefleri ise, ürünlerin veya hizmetlerin hiçbir hata yapmadan üretilmesini hedefleyen bir yaklaşımdır.
Genel olarak, kalite kontrol süreci, bir ürün veya hizmetin kalitesinin belirlenmesi, belirlenen kalite standartlarına uygunluğunun kontrol edilmesi ve hataların tespit edilip düzeltilmesi için önemli bir süreçtir. Bu süreçte kullanılan yöntemler ve araçlar, hataların minimum düzeye indirgenmesine ve üretim sürecinde kalitenin artırılmasına yardımcı olmaktadır.
Alt Alt Alt Başlık: Yüzde Hata Oranı
Endüstriyel mühendislikte kalite kontrol süreçleri, üretim hatalarının azaltılmasına ve kalitenin artırılmasına yönelik önemli bir unsurdur. Bu süreçlerde kullanılan yüzde hata oranı, bir ürünün veya hizmetin üretiminde meydana gelen hataların oranını gösteren bir metriktir. Yüzde hata oranı, genellikle bir üretim dönemi boyunca üretilen ürünlerdeki hataları tespit etmek için kullanılır ve bu hataların türüne, sayısına ve sıklığına göre raporlanır. Elde edilen veriler, kalite kontrol sürecinin geliştirilmesi ve hataların ortadan kaldırılması için kullanılır.
Yüzde hata oranı, basit bir hesaplama ile belirlenir. Üretilen ürün sayısı ve bu ürünlerin arızalı sayısı bilindiğinde hesaplama yapılarak yüzde hata oranı bulunur. Bu oranın düşürülmesi için hata kaynakları tespit edilir ve çözümler geliştirilir.
Alt Alt Alt Başlık: Pareto Analizi
Pareto Analizi, endüstriyel mühendislikte kalite kontrol sürecinde kullanılan önemli bir araçtır. Bu analiz yöntemi, üretim süreçlerinde meydana gelen hataların yüzde oranını belirlemek için kullanılır. Pareto analizi, 80/20 prensibi olarak da bilinen Pareto ilkesine dayanarak, üretim sürecindeki hataların büyük bölümünün birkaç ana nedenle ilişkili olduğunu ve diğer nedenlerin etkisinin düşük olduğunu varsayar.
Pareto analizinde, belirli bir süre içindeki hataların türü ve nedenleri kaydedilir ve bu veriler Pareto diyagramına dönüştürülür. Diyagramda, hataların yüzde oranı azdan çoğa doğru sıralanır ve her bir hatanın nedeni gösterilir. Bu analiz yöntemi sayesinde, üretim sürecindeki hataların yüzde oranı kolayca belirlenebilir ve kaynaklar daha etkin bir şekilde kullanılabilir.
- Pareto analizi, üretim sürecindeki hataların kaynağını belirlemeyi kolaylaştırır ve bu sayede hataların nedenleri daha hızlı bir şekilde ortadan kaldırılabilir.
- Bu analiz yöntemi, üretim sürecindeki kaynakları daha etkin bir şekilde kullanmanızı sağlar ve üretimdeki verimliliği artırır.
Pareto analizi, endüstriyel mühendislikte önemli bir yere sahip olmasının yanı sıra diğer sektörlerde de kullanılan bir analiz yöntemidir. Bu nedenle, Pareto analizi yöntemlerinin ve kullanımlarının detaylı bir şekilde öğrenilmesi, işletmelerin kalite yönetiminde önemli bir avantaj sağlayacaktır.
Alt Alt Başlık: İlk Örnek Kontrolü (IPC)
İlk Örnek Kontrolü (IPC) işlemi, üretim sürecinin başlangıcında ürünlerin kalitesinin kontrol edilmesi amacıyla kullanılır. Bu işlem, üretime başlamadan önce bir örnek ürünün kalitesi kontrol edilerek kalite standartlarının uygunluğu sağlanır. IPC işlemi, üretim sürecinde hataların oluşmasını engeller ve oluşan hataların düzeltilmesi için bir fırsat sunar.
IPC işlemi, üretim sürecindeki ilk adımda uygulanır ve üretim hattında meydana gelen hataların önüne geçer. ISO 9001 standardı tarafından da desteklenen IPC işlemi, ürün kalitesinde artış sağlar ve müşteri memnuniyetini artırır. IPC işlemi genellikle, üretim hattına yeni bir ürünün eklenmesi ya da üretim sürecinde önemli değişiklikler yapılması durumlarında kullanılır.
IPC işlemi, üretim sürecindeki hataları önleyerek ürün kalitesini artırdığı gibi, maliyetleri de azaltır. Üretim sürecinin başında hataların tespit edilmesi, maddi kayıpların ve zaman kaybının önüne geçer. Ayrıca, IPC işlemi sayesinde üretim sürecindeki hatalar daha az oluşur ve kalite kontrol maliyetleri düşer.
Bir IPC işlemi sırasında, üretim sürecinde kullanılan malzemeler ve ekipmanlar kontrol edilir. Üretim sürecindeki her adım detaylı bir şekilde incelenir ve hataların doğru bir şekilde tespit edilmesi için gerekli önlemler alınır. IPC işlemi sayesinde, üretim sürecinde oluşabilecek hataların tespit edilmesi daha kolay hale gelir ve üretim sürecindeki kalite standartları daha iyi bir şekilde korunur.
Üçüncü Alt Başlık: Tasarım Deneyleri
Tasarım deneyleri, ürün veya hizmetlerin tasarımında olası sorunları tespit ederek, bunları ortadan kaldırmak için kullanılan sistemli bir yöntemdir. Bu yöntemde, belirli bir tasarımın özellikleri değiştirilerek farklı senaryolar simüle edilir ve sonuçları ölçülür. Bu sayede olası problemler tespit edilir ve düzeltilir, böylece ürün veya hizmet son kullanıcıya mükemmel bir kalite ve performans sunar.
Tasarım deneylerinin çeşitli avantajları vardır. Öncelikle, tasarımların gerçek ortamlarda test edilmesi, ürün veya hizmetin kalitesini artırır ve müşteri memnuniyetini artırır. Ayrıca, tasarımın tüm yönleri önceden test edilerek, üretim maliyetleri düşürülür ve zaman kaybı önlenir. Tasarım deneyleri ayrıca, ürün veya hizmetin rekabet avantajını artırır, çünkü ürünün tasarımında olası sorunları tespit etme ve çözme kabiliyeti rakiplerden farklılaşır.
Tasarım deneyleri farklı yöntemlerle uygulanabilir. Bu yöntemler arasında prototip yapma, kullanılabilirlik testleri, kullanıcı deneyimi testleri, hız testleri, performans testleri gibi testler yer alır. Yapılan testler sonucunda elde edilen veriler, tasarım sürecinde kullanılarak ürün veya hizmetin kalitesi artırılır.
Bir diğer önemli nokta, tasarım deneylerinin doğru bir şekilde uygulanmasıdır. Bu nedenle, tasarım deneyleri süreci belirli bir disiplin içinde olmalıdır. Bu disiplin içinde tasarım sorunlarının doğru şekilde tanımlanması, analiz edilmesi ve düzeltilmesi önemlidir. Doğru uygulandığında, tasarım deneyleri ürün veya hizmet tasarımında birçok fayda sağlar.