Programlanabilir mantık kontrolleri, otomasyon sistemlerinin geliştirilmesinde son derece önemlidir Bu eğitim ile hem programlanabilir mantık kontrolleri hem de sistem geliştirme konularına hakim olacaksınız Kendinizi geliştirmek için şimdi kaydolun!
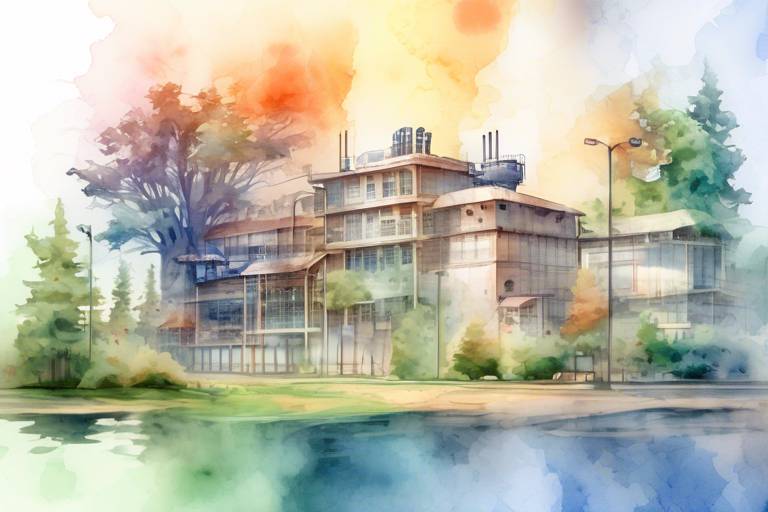
Endüstriyel otomasyon sistemleri, işletmelerin üretim sürecinde önemli bir rol oynamaktadır. Bu süreçte akıllı, esnek, hızlı ve güvenilir bir kontrol sistemi gerekmektedir. Programlanabilir Mantık Kontrolleri (PLC), bu ihtiyacı karşılamak için tasarlanmış bir elektronik kontrol cihazıdır.
Bu makalede, programlanabilir mantık kontrol sistemleri ile ilgili konular ele alınacak ve sistemi geliştirmek için gerekli adımlar incelenecektir. Makalede, PLC'ler, işlevleri, faydaları, nasıl çalıştıkları, farklı tipleri ve kullanım amaçları gibi konular tartışılacaktır. Ayrıca, PLC sistemlerinin tasarımı ve geliştirilmesi, endüstri 4.0 uygulamaları, sayım sistemleri ve veri toplama ve analizi gibi konulara da değinilecektir.
Programlanabilir Mantık Kontrolleri Nedir?
Programlanabilir mantık kontrolü (PLC), endüstriyel kontrol uygulamaları için özel bir bilgisayar sistemidir. PLC'ler, belirli bir işlevi gerçekleştirmek için programlanabilen bir mikroişlemci, giriş ve çıkış modülleri ve çeşitli iletişim portları içerir. PLC kullanımı, endüstriyel otomasyon süreçlerini daha etkili, güvenli ve verimli hale getirir.
PLC'ler birçok işlevi yerine getirir. Programlanabilir mantık kontrolü, endüstriyel süreçlerde hep kullanılmaktadır. PLC'ler sayesinde üretim süreçleri otomatik hale getirilir ve maliyetler düşürülür. Ayrıca, PLC'ler kablolama ihtiyacını azaltır, alanları optimize eder ve hatanın giderilmesi kolaylaşır. PLC'ler aynı zamanda yüksek performans, kesintisiz işlevsellik ve daha hızlı yanıt süresi sunar.
PLC İşlevleri |
---|
Endüstriyel kontrol süreçleri |
Üretim hatları ve makinelerinin otomasyonu |
Geri bildirim ve kontrol sistemleri |
Hareket kontrol sistemleri |
PLC'lerin birçok faydası vardır. Bunların arasında, üretim hatlarının daha etkin kullanılması ve verimlilik artışı, daha az bakım ihtiyacı ve daha kısa yanıt süreleri yer alır. Ayrıca, PLC'lerin kullanımı üretim hatalarının %100 denetimini sağlar. Hatanın giderilmesi kolaylaşır, diğer kontrol sistemlerine göre daha az yer kaplar, daha güvenilir ve daha esnek bir sistem sunar.
- Üretim hattı maliyetlerinin azaltılması
- Hızlı yanıt zamanları
- Yüksek güvenilirlik
- Diğer kontrol sistemlerine göre daha az yer kaplama
- Toplam kontrol seçenekleri
PLC Sistemleri Nasıl Çalışır?
PLC'ler (Programlanabilir Mantık Kontrolörleri), otomasyon sistemlerinde kullanılan dijital cihazlardır. Sinyalleri okur, işler ve çıktı verirler. Olağanüstü yetenekleri sayesinde, modern otomasyon sistemlerinin en önemli parçalarından biridirler.
PLC'ler, başka bir deyişle, içeriklerini programlanabilir şekilde değiştirebileceğimiz dijital cihazlar olarak tanımlanabilirler. Bu özelliği, endüstriyel sistemlerde farklı işler yapmak üzere programlanmış fonksiyon bloklarını içerebilmelerini sağlar. Örneğin, sıcaklık kontrolü, basınç kontrolü ve hız kontrolü gibi farklı işlemler bu bloklar aracılığıyla programlanabilir.
PLC'lerin iki temel bileşeni vardır: CPU (Merkezi İşlem Birimi) ve I/O (Giriş/Çıkış) modülleri. CPU, programlamayı okuyan ve yorumlayan, kontrol işlemini gerçekleştiren cihazın beynidir. I/O modülleri ise doğrudan cihazın giriş/çıkış aygıtları ile bağlantılıdır ve bu aygıtlardan gelen sinyalleri okur.
PLC'lerin çalışma modları, ön yüklemeli mod ve çalıştırma modudur. Ön yüklemeli mod, programlanabilir işlemciye yüklenecek programların hazırlanmasıdır. Çalıştırma modu ise, yüklenen programların çalıştırılmasıdır. Bu programlama dilleri, merdiven diyagramları, fonskiyon blokları ve yapısallık yöntemi olarak adlandırılır.
PLC sistemlerinin çalışma özellikleri, programlanabilir ve entegre edilebilir olmaları sayesinde endüstriyel sistemler için çok önemlidir. Bu özellikler, küçük bir PLC sisteminden büyük bir sanayi tesisine kadar birçok farklı uygulama için kullanılabilir hale gelmiştir.
PLC Programlama Dilleri
PLC programlama dilleri, endüstriyel otomasyon uygulamaları için çok önemli bir role sahiptir. PLC programlama dilleri, PLC programları için kullanılan çeşitli grafiksel ve yazılısel dillerdir. Endüstriyel otomasyon sistemlerinde yaygın olarak kullanılan üç temel PLC programlama dilinden bahsedebiliriz:
- Merdiven Diyagramı
- Fonksiyon Blokları
- Yapısallık Metodu
Merdiven diyagramı, merdiven basamaklarına benzeyen bir grafiksel programlama dili kullanır. Bu dil, elektriksel kontrol devrelerinin mantıksal kontrollerinin yazılımını yapmak için en yaygın olarak kullanılan programlama dilidir. Fonksiyon blokları, temel matematik işlevlerini içeren küçük blokları kullanarak PLC programlarını yazmak için kullanılır. Bu dil, yazılım geliştiricilere yazılım tasarlama ve geliştirme sürecinde daha fazla esneklik sağlar. Yapısallık metodu ise, C gibi yapısal programlama dillere benzer ve PLC programları yazmak için kullanılır.
PLC programlama dillerinin kullanımı, endüstriyel otomasyon sistemlerinin karmaşıklığını azaltmaya yardımcı olur. Programlama dilleri, endüstriyel otomasyon uygulamalarında en uygun yaklaşımın kullanılmasını sağlar ve hataları minimize eder. Ayrıca, programlama dilleri sayesinde, endüstriyel otomasyon sistemlerindeki verimlilik artar ve işletmeler daha düşük maliyetle daha fazla üretim yapabilirler.
PLC CPU
Makine kontrolü ve otomasyon uygulamaları için kullanılan Programlanabilir Mantık Kontrolleri (PLC), karmaşık süreçleri sıralı işlemlere dönüştürmek amacıyla tasarlanmıştır. PLC sistemleri, merkezi bir işlemciden, giriş/çıkış modüllerine kadar birçok bileşeni içerir. PLC CPU, temel olarak bir bilgisayar işlemcisine benzer ve merkezi işlemi gerçekleştirir.
PLC CPU'larının farklı çeşitleri vardır ve her bir çeşidin belirli özellikleri bulunmaktadır. Bazıları yüksek hızlı çalışma yeteneğine sahipken, diğerleri daha ekonomik maliyetlerle daha az performans sağlamaktadır. Ayrıca, PLC CPU'ları üzerinde bağlı olduğu I/O modüllerine ve diğer bileşenlere göre farklı özelliklere sahiptir.
PLC sistemleri, yüksek performanslı işlemler gerçekleştirebilen, gelişmiş bellek sistemleri ve işletim sistemleri ile donatılmış olan CPU'lar kullanır. Bu bileşenler, farklı programlama dilleri kullanılarak programlanabilir. PLC programlama dilleri arasında merdiven diyagramı, fonksiyon blokları ve yapısallık metodu yer alır.
PLC CPU'ların performans kriterleri, hızlı, güvenilir ve doğru sonuçlar elde etmek için önemlidir. Bir PLC sistemi tasarlarken, ihtiyaç duyulan performans özellikleri belirlenmeli ve doğru CPU seçimi yapılmalıdır. Ayrıca, güçlü bir CPU seçimleri, sistemde birden fazla görevi aynı anda gerçekleştirme yeteneği sağlayabilir.
Sonuç olarak, bir PLC sistemi için doğru CPU seçimi yapmak, sistem performansının güvenliğini ve etkinliğini sağlamak için oldukça önemlidir. Bu nedenle, CPU çeşitleri, özellikleri ve performans kriterleri hakkında doğru bilgiye sahip olmak, mükemmel bir PLC sistem tasarımı ve geliştirilmesi için temel şarttır.
PLC I/O Modülleri
PLC sistemlerinde I/O modülleri, PLC kontrolörü ve harici cihazlar arasındaki veri iletişimini sağlarlar. Bu modüller, ana kontrolör tarafından veri toplama ve çıkış verilerini işleme işlevlerini yerine getirirler. I/O modülleri 2 ana kategoriye ayrılır:
- Dijital I/O Modülleri
- Analog I/O Modülleri
Dijital I/O modülleri, 0 veya 1 şeklinde kulllanılabilen basit veri sinyallerinin işlenmesinde kullanılırken, analog I/O modülleri açık ve kapalı aralıklarla veri toplamayı sağlarlar. Tasarım gereklilikleri, genellikle sistem performansı, veri çözünürlüğü, güvenilirlik ve yedeklilik durumunu kapsar.
Veri iletim yöntemi, mevcut sistem gereksinimlerine bağlı olarak birkaç farklı şekilde gerçekleştirilebilir:
- Seri Bağlantı
- Paralel Bağlantı
- EtherNet/IP
- Profibus
Seri bağlantı durumunda veri, tek bir hattan bir cihazdan diğerine gönderilir. Bu yöntem, veri iletiminde düşük hızlara neden olabilir ve doğru bir şekilde veri iletimi için uygun bir protokol gerektirir. Paralel bağlantı, verinin birden fazla hattan aktarılmasını sağlar ve daha yüksek hızlara izin verir. Ancak, geleneksel olarak daha pahalı ve araştırma ve tasarım gerektirir.
EtherNet/IP ve Profibus, endüstriyel iletişim ağları olarak bilinir ve PLC sistemleri için veri iletiminde yaygın olarak kullanılır. Özellikle endüstriyel sistemlerle uyumludurlar ve daha yüksek hızlarda ve verimlilikte veri iletimi sunabilirler.
PLC Çalıştırma Modları
PLC'lerin farklı çalıştırma modları vardır. Bu modlar, cihazların programlanabilir özelliklerinin farklı şekillerde kullanılmasını sağlar ve buna bağlı olarak daha geniş bir veri yelpazesi toplanır.
Ön yüklemeli mod, PLC'nin önceden yüklenmiş programların çalıştırılması için tercih edilen bir moddur. Bu modda, PLC'de bulunan tüm önceden yüklenmiş programların aynı anda yürütülmesi ve bir programa ihtiyaç duyulduğunda seçilmesi mümkündür. Bu mod, daha hızlı bir tepki süreci sağlar ve özellikle acil durumlarda kullanılır.
CPU tarihçesi, PLC sistemlerinin evrimiyle ilgili önemli bir konudur. PLC'ler ilk kez 1968 yılında Otomatik Kontrol Konferansı'nda tanıtıldı. Bu cihazların temel amacı, motorların hızını kontrol etmekti. Daha sonra, PLC'ler çeşitli endüstriyel uygulamalar için kullanılmaya başlandı. Sürekli olarak CPU'lar güncellendi ve geliştirildi. Bugünün PLC'leri, farklı işlevleri yerine getirebilen yüksek performanslı CPU'larla donatılmıştır.
PLC cihazları, arayüzlerini seçmek için farklı seçenekler sunar. Bu arayüzler, standart dokunmatik ekranlardan uzaktan erişimli internet tarayıcılarına kadar geniş bir yelpazeye sahiptir. Bu arayüzler, kullanıcıların cihazı kontrol etmelerini, programlarını yüklemelerini ve verileri izlemelerini sağlar. Ayrıca, bu arayüzler, diğer cihazlarla iletişim kurmaya ve verileri aktarmaya da yardımcı olabilir.
PLC sistemlerinin çalıştırma modları, endüstriyel ihtiyaçlara göre tasarlanmıştır. Bu modlar, cihazların sürekli çalışmasına yardımcı olurken, aynı zamanda daha hızlı ve güvenli bir çalışma ortamı sunar.
PLC Sistem Tasarımı ve Geliştirme
PLC Sistem Tasarımı ve Geliştirme, PLC bileşenlerinin doğru seçimi, sistem planlaması ve entegrasyonu hakkında bilgi veren önemli bir konudur.
PLC bileşenleri arasında, CPU, I/O modülleri, güç kaynakları ve veri depolama cihazları yer alır. Doğru bileşenleri seçmek, PLC sisteminin doğru çalışmasını ve istenen sonuçları elde etmeyi sağlamak için hayati önem taşır. CPU seçimi, performans kriterlerine ve sistem ihtiyaçlarına bağlı olarak yapılmalıdır. I/O modül çeşitleri, tasarım gereklilikleri ve veri iletim yöntemleri konusunda dikkatli bir analiz yapılmalıdır. Ayrıca, güç kaynakları ve veri depolama cihazları da doğru seçilmelidir.
Sistem planlaması, PLC sistemi ihtiyaç analizi, sistem gereklilikleri ve tasarım belgeleri gibi önemli unsurları içerir. İhtiyaç analizi, mevcut problemlerin ve ihtiyaçların belirlenmesi ve fonksiyonel gereksinimlerin tanımlanması işlemidir. PLC sistemi gereklilikleri, tasarımın belirlenmesi için önemli bir faktördür. Tasarım belgeleri, devre şemaları ve etherCAT topolojisi gibi belgeleri içerir.
PLC sistemi entegrasyonu, PLC sistemlerinin mevcut sistemlere entegrasyonu ve veri alışverişi protokolleri gibi konuları içerir. Bu entegrasyon, veri alışverişi protokolleri kullanılarak yapılabilir. PLC sistemi, entegre bir sistem için de önemlidir. Bu, tüm bileşenlerin birbirleriyle uyumlu çalışmasını ve sistemin doğru şekilde çalışmasını sağlar.
PLC Bileşen Seçimi
PLC sistemleri, endüstriyel otomasyonun yanı sıra, çeşitli sektörlerde de kullanılmaktadır. Bu sistemlerin her bir bileşeni, belirli bir amaç doğrultusunda seçilmelidir.
PLC'nin CPU bileşeni, sistemin ana işlemcisidir ve program kodlarını yürütür. CPU, işlemci hızı, bellek boyutu ve işletim sıcaklığı gibi özellikleri açısından farklılık gösterir. Doğru CPU seçimi, sistemin başarılı bir şekilde çalışması için önemlidir.
I/O modülleri, PLC sisteminin çevre birimlerini kontrol etmesini sağlar. Giriş/çıkış modülleri, analog/dijital modüller veya özel modüller gibi farklı türlerde mevcuttur. İhtiyaca göre doğru I/O modül çeşidi seçilmelidir.
PLC sistemlerinin çalışması için güç kaynakları gereklidir. Güç kaynakları, doğru voltajda işlemek için gerekli olan enerjiyi sağlar. Güç kaynaklarında, giriş gerilimi, çıkış gerilimi ve güç faktörü gibi önemli özelliklere dikkat edilmelidir.
Veri depolama cihazları, sistemin verilerini saklamak için kullanılır. Doğru veri depolama aygıtını seçmek, sistemin doğru şekilde çalışması için önemlidir. Veri depolama cihazları arasında, floppy disketler, CD'ler, flash bellekler, hard diskler, vb. mevcuttur.
PLC bileşenlerinin doğru bir şekilde seçilmesi, sistemin doğru şekilde çalışmasını sağlar. Yapılan yanlış bir bileşen seçimi, sistemin verimliliğini ciddi şekilde etkileyebilir. Bu yüzden, bileşen seçiminde dikkatli ve doğru bir şekilde hareket etmek gerekmektedir.
Sistem Planlama
PLC sistemleri, işletmelerdeki üretim ve süreçleri kontrol etmek için kullanılan endüstriyel otomasyon sistemleridir. Herhangi bir PLC sistemi tasarımı öncesi ihtiyaç analizi yapılması gerekmektedir. Bu ihtiyaç analizi sayesinde hangi özelliklere sahip bir PLC sistemi gerektiği belirlenir.
PLC sistemi ihtiyaç analizinde öncelikle tesislerdeki mevcut süreçler ve üretim hattı yapısı incelenir, hangi kontrollerin yapılması gerektiği belirlenir. Bu sayede hangi giriş/çıkış modüllerinin kullanılacağı, hangi çıkışlar ve sensörlerle çalışılacağı tespit edilir.
PLC sistemi tasarımı sırasında sistem gereklilikleri de belirlenir. Bunlar genellikle giriş/çıkış sayısı, hızı, kullanılacak dil, işletim sistemi gibi teknik gereklilikleri kapsar. Sistem gereklilikleri doğru belirlenmezse, verimli bir çalışma beklenemez.
PLC tasarımı sırasında ayrıntılı tasarım belgeleri hazırlanır. Bu belgeler, PLC sistemi tasarımının her aşamasında kullanılan donanım ve yazılım bileşenlerini belirtir. Ayrıca PLC sistemi kurulumu, bakımı ve onarımını kolaylaştırmak için tasarım belgelerinde, elektrik şemaları, donanım bileşenleri, yazılım ve açıklamalar gibi ayrıntılı bilgiler yer alır.
Sonuç olarak, sistemin tam olarak nasıl kontrol edileceği, hangi verilerin toplanması gerektiği, bu verilerin hangi cihazlarla işleneceği ve son olarak, nasıl bir veri raporu oluşturulacağı gibi birçok detay belirtilir. Tüm bu bilgiler doğru bir şekilde hazırlanan sistemi, istenilen işlevleri yerine getirmesi için hazırlama açısından oldukça önemlidir.
Entegrasyon
PLC sistemleri, mevcut endüstriyel sistemlerle birleştirilerek kullanılabileceği gibi birçok sistemle de entegre edilebilir. Entegrasyonun amacı, PLC sistemlerinin çalışma esnekliklerini artırmak, işyerinde verimliliği artırmak ve mevcut ekipmanın kullanım ömrünü uzatmaktır. PLC entegrasyonu, veri alışverişi protokolleri kullanılarak gerçekleştirilebilir.
PLC'ler, otomasyon sistemleri aracılığıyla iletişim kurabilen birçok farklı protokolü destekler. Ancak, profesyonel otomasyon şirketleri, birçok farklı endüstriyel protokolü destekleyen bir cihaz olarak bilinen "gateway" kullanmayı tercih eder. Gateway, farklı protokoller arasında veri alışverişine izin veren bir cihazdır. PLC'ler gibi endüstriyel sistemler, genellikle Modbus, SNMP, EGD ve Ethernet protokollerini desteklemektedir. PLC entegrasyonunun anahtar bileşenleri arasında, entegre kontrol sistemleri için uygun bir veri tabanı yönetim sistemi gereklidir.
PLC sistemlerinin entegrasyonu birçok avantaj sunar. Entegrasyon, sistemle ilgili verileri analiz etme veya kontrol etme yeteneği sağlayarak işletme verimliliğini artırır. Ayrıca, PLC'nin entegrasyonu, otomasyonu artırarak insan hatası oranını da büyük ölçüde azaltabilir. PLC entegrasyonu, işletmelerin daha akıllıca kararlar almasına ve işletme süreçlerini daha da optimize etmesine olanak tanır.
PLC Sistemleri ve Endüstri 4.0
Endüstri 4.0, sanayide dijitalleşme ve otomasyonun bir sonucu olarak ortaya çıkmış bir terimdir. İşletmelerin verimliliği artırmak ve iş süreçlerini optimize etmek için dijital teknolojilere dayalı sistemlere geçişi ifade eder. Bu noktada, PLC sistemleri de endüstri 4.0 çerçevesinde önemli bir rol oynamaktadır.
PLC sistemleri, otomasyonun temel yapı taşlarıdır. Endüstri 4.0'ın vizyonu ve hedefleri ile uyumlu bir şekilde, PLC sistemleri daha akıllı, daha bağlantılı ve daha esnek hale getirilerek iş süreçlerini optimize edebilirler. PLC sistemleri, endüstri 4.0 için önemli bir veri kaynağıdır. Bununla birlikte, PLC'ler, veri toplama ve analizinde kullanılan veri toplama sistemleri ile entegre edilerek daha akıllı ve daha dinamik bir endüstriyel üretim ortamı sağlarlar.
PLC sistemleri ile otomatik depolama, sensör kontrollü üretim gibi endüstri 4.0 uygulamaları gerçekleştirilebilir. Akıllı fabrikalar, üretimde daha fazla verimlilik ve daha az hata ile sonuçlanacak şekilde tasarlanan, üretimi optimize etmek için çeşitli sensörler ve sistemleri entegre eden bir endüstri 4.0 uygulamasıdır.
PLC sistemleri, endüstri 4.0'ın bir diğer önemli uygulama alanı olan sayaçlarla da entegre edilebilir. PLC sistemleri kullanılarak sayaç sistemleri tasarlamak ve uygulamak, endüstriyel üretim süreçlerinde önemli bir rol oynar. Ayrıca, sayım sistemleri ile üretim ürünlerinin miktarları, üretim hızları gibi veriler toplanabilir ve analiz edilebilir. Böylece, üretim süreçleri daha iyi yönetilebilir.
Sonuç olarak, PLC sistemleri endüstri 4.0'ın önemli bir parçasıdır ve diğer endüstriyel sistemlerle entegrasyonu iş süreçlerinde büyük bir fark yaratır. PLC sistemleri, işletmelerin üretim verimliliğini artırmalarına, maliyetleri düşürmelerine ve daha verimli bir üretim süreci sağlamalarına yardımcı olabilir.
Endüstri 4.0 Nedir?
Endüstri 4.0, akıllı üretim sistemlerini kullanarak gelecekteki üretim süreçleri için bir vizyon olarak tanımlanabilir. Bu vizyonda, IoT (Nesnelerin İnterneti), veri analizi, anahtar performans göstergeleri ve dijitalleştirme teknolojileri kullanılarak üretim verimliliği artırılmayı hedeflenir. Endüstri 4.0 sadece üretim süreçlerinin daha verimli hale getirilmesi değildir, aynı zamanda yeni ekonomik fırsatlar yaratarak daha sürdürülebilir bir gelecek sağlamayı amaçlar.
Endüstri 4.0 vizyonunda, işletmeler daha hızlı, daha güvenilir ve daha esnek bir şekilde üretim yapabilir. Bu sayede müşteri memnuniyeti artar ve işletmeler arasındaki rekabet avantajı kazanılır. Ayrıca, endüstri 4.0, işletmelerin üretim süreçlerinde daha akıllı kararlar almasını sağlayarak üretim maliyetlerini azaltır ve kaynak kullanımını daha verimli hale getirir. Bunun yanı sıra, endüstri 4.0 ile birlikte işletmelerin üretim süreçleri daha çevre dostu hale gelir, sürdürülebilir bir gelecek için katkı sağlanır.
- Endüstri 4.0 vizyonu, üretim süreçlerini daha akıllı hale getirerek verimliliği artırmayı hedefler.
- İşletmeler bu vizyon sayesinde daha hızlı, daha güvenilir ve daha esnek üretim yapabilir.
- Endüstri 4.0 aynı zamanda daha sürdürülebilir bir geleceğe yönelik ekonomik fırsatlar yaratır.
- Üretim süreçlerinde daha akıllı kararlar alındığı için maliyetler azalır ve kaynak kullanımı daha verimli hale gelir.
Endüstri 4.0, ciddi bir dönüşüm sürecidir ve işletmelerin rekabet avantajı kazanması için kabul etmeleri gereken bir gerçektir. Bu nedenle, işletmelerin endüstri 4.0 vizyonunu benimsemeleri, dijitalleşmeyi hızlandırmaları, teknolojik yatırımlar yapmaları ve üretim süreçlerini daha verimli hale getirmeleri gerekmektedir.
PLC ve Endüstri 4.0 Uygulamaları
Endüstri 4.0, giderek akıllılaşan fabrikalar, otomatik depolama sistemleri ve sensör kontrollü üretim gibi yenilikçi uygulamalara yol açıyor. PLC sistemleri büyük ölçüde bu uygulamaların arkasındaki teknolojinin temelini oluşturuyor. Bu uygulamalara bir göz atalım:
Akıllı Fabrikalar | Otomatik Depolama | Sensör Kontrollü Üretim |
---|---|---|
Akıllı fabrikalar, otomatik işletim sistemleriyle birlikte çalışan tam otomatik tesislerdir. Bu sistemler, üretim verimliliğini önemli ölçüde artırabilir ve üretim sürecindeki hataların sayısını azaltabilir. PLC sistemi, bireysel bileşenlerin otomatik olarak çalışmasına yardımcı olurken, aynı zamanda aralarındaki senkronizasyonu sağlar. | PLC sistemleri, otomatik depolama sistemlerinin geliştirilmesinde çok önemli bir rol oynar. Otomatik depolama sistemleri, ürünlerin hızlı ve verimli bir şekilde depolanmasını ve çıkarılmasını sağlar. Tüm depolama işlemleri, PLC'ler üzerinden yönetilir. Bu sayede operatör yanlışlıkla yanlış ürünleri seçme veya ürünleri yanlış yerlere yerleştirme hatasını en aza indirir. | PLC sistemleri, sensör kontrollü üretimde en önemli bileşenlerin arasında yer alır. Sensörler sayesinde, üretim hattındaki her bir parça anlık olarak kontrol edilebilir. PLC sistemi, bu verileri okuyabilir ve üretim hattındaki herhangi bir problemi hızlıca tespit edip çözebilir. Bu sayede, üretim maliyetleri düşürülür ve verimlilik artırılır. |
PLC sistemleri, endüstri 4.0'ın belkemiğini oluşturuyor ve akıllı fabrikalar, otomatik depolama ve sensör kontrollü üretim gibi yenilikçi uygulamalar üretildikçe bu teknolojinin önemi daha da artacaktır.
PLC Sistemleri ve Sayaçlar
Sanayideki birçok uygulama, hammadde kullanımı, üretim miktarı ve verimlilik takibini gerektirir. Bu takibin yapılabilmesi için, bir sayaç veya sayım sistemi kullanmak gereklidir. Ancak sayım işlemlerinin çok sayıda yapılması insan hatalarına sebep olabilir. İşte burada PLC sistemleri devreye girerek, doğru ve hatasız bir sayım işlemi gerçekleştirmek mümkün olur.
PLC sistemleri, sanayide yaygın bir şekilde kullanılırken, sayım işlemlerinde de sıklıkla tercih edilen bir seçenektir. Çünkü PLC'lerin programlanabilir mantık kontrol özellikleri sayesinde, sayım işlemleri programlanabilir ve otomatik hale getirilebilir.
Sayaçların özellikleri ve kullanım alanlarına göre farklı tasarımları ve çeşitleri vardır. PLC sistemleri ile yapılan sayım sistemi tasarımı da, kullanılan sayaçların özelliklerine göre farklılık gösterir. PLC sistemleri, sayma ve ölçme işlemleri için kullanılan sayaçlarla çeşitli sinyal kaynaklarına bağlanarak kullanılabilir.
PLC'ler, sayım işlemleri için kullanılan sayaçlarla birlikte, hareket sensörleri, hız sensörleri, basınç sensörleri gibi diğer çeşitli sensörlerle de entegre çalışabilir. Bu sayede sayım işlemleri, üretim süreci boyunca otomatik olarak gerçekleştirilir ve hataların önlenmesine yardımcı olur.
Sayım sistemi tasarımında, seçilen sayaçlarının doğruluğu ve doğru bir şekilde sinyal kaynağına bağlanması son derece önemlidir. PLC sistemleri ile sayaçların doğru bir şekilde bağlantıları yapılarak, doğru ölçüm sonuçları elde edilebilir. Sayaçların verilerinin, PLC sistemlerinde çalışan özel yazılımlar yardımı ile işlenerek depolanması, sonrasında veri analizi için kullanılabilir.
Sayaçların Özellikleri
PLC sistemleri kullanılarak sayım sistemleri tasarlanıp uygulanabilir. Bu sistemin temelinde olan sayacın özellikleri şöyle sıralanabilir:
Sayaç Tipleri | Sayaç Sinyal Kaynakları | Sayaç Doğruluğu |
---|---|---|
Elektronik sayacı, mekanik sayacı, gaz sayacı, su sayacı gibi farklı tiplerde sayaçlar kullanılabilir. | Sayaçların sinyal kaynakları arasında modbus haberleşme protokolü, RS-232/485 seri haberleşme, Ethernet bağlantısı, analog sinyaller ve dijital toplama cihazları gibi farklı seçenekler bulunur. | Sayaç doğruluğu seçilen tip ve modele göre değişir. Örneğin elektrik sayacı %1-2, su sayacı ise yaklaşık %3-5 arasında bir doğruluğa sahiptir. |
Sayaçların işlevleri, kullanım alanları ve özellikleri sistemin tasarımı için önemli bir yere sahiptir. Bu bilgilerin doğru bir şekilde öğrenilerek, sayaçlı PLC tasarımı ve uygulaması başarılı bir şekilde gerçekleştirilebilir.
PLC Sistemleri ile Sayım Sistemi Tasarımı
PLC'ler, sayım sistemlerinin tasarımı ve uygulamasında yaygın olarak kullanılmaktadır. Sayım sistemleri, sayaçlarla veri toplama, depolama ve işlemeye dayalı uygulamalardır. PLC'ler, sayım sistemlerinin kontrolü ve idaresine olanak sağlar. Bu bölümde PLC sistemleri kullanılarak sayım sistemi tasarımı ve uygulaması hakkında bilgi verilecektir.
Sayım sistemleri için uygun sayaç tipi seçmek çok önemlidir. Sayaçlar, farklı sinyal kaynaklarından gelen verileri ölçmek için kullanılır. Sayım sistemi tasarımı, sayaçların doğru bir şekilde bağlanmasını gerektirir. PLC ile sayım sistemleri oluşturmak için, PLC'nin dijital giriş ve çıkış (I/O) modülleri kullanılır. Sayaçların sinyali, dijital girişlere doğrudan bağlanabilir veya sensörlerle birlikte kullanılabilir.
Sayaç sinyalleri, yüksek hızlı sayaçlar tarafından toplanabilir. Bu sinyaller daha sonra işlenip değerlendirilir ve sonunda bilgiye dönüştürülürler. PLC'ler, sayım sistemlerinde kullanılan sayaçların, farklı sinyal kaynaklarından gelen verileri işleyebilmesini sağlar. Sayaç sinyalleri, PLC kontrol yazılımı tarafından doğrudan okunabilir ve işlenebilir.
Sayım sistemleri, endüstriyel sayım uygulamalarında yaygın olarak kullanılır. Bu uygulamalar arasında otomatik sayım, verimlilik ölçümü, kalite kontrol ve envanter takibi yer alır. Uygun bir PLC sistemi seçerek ve sayaçlar ile sensörlerin doğru bir şekilde bağlanmasını sağlayarak, endüstriyel sayım uygulamaları başarıyla gerçekleştirilebilir.
Bir endüstriyel sayım uygulaması olarak, üretim hattındaki bir makinede kullanılan parça sayısını saymak için bir sayım sistemi tasarlayabilirsiniz. Bu sayım sistemi, makineye entegre edilmiş bir sayaç kullanılarak gerçekleştirilebilir. Sayım verileri, PLC'nin giriş modüllerine bağlı dijital giriş sensörleri aracılığıyla toplanır ve işlenir. Bu sayede, makine üretim verimliliği ve envanter takibi gibi konularda doğru bilgiler elde edilebilir.
PLC Sistemleri ile Veri Toplama ve Analizi
Programlanabilir mantık kontrolleri (PLC) endüstriyel otomasyon sistemlerinde yaygın olarak kullanılmakta ve sadece veri toplama ve kontrol fonksiyonları ile sınırlı kalmamaktadır. PLC sistemleri ayrıca birçok veri toplama sensörü aracılığıyla veri toplayabilir, farklı veri işleme algoritmaları ile bu verileri işleyebilir ve ardından verimliliği artırmak için kullanılabilir.
Veri toplama, özellikle endüstriyel ortamlarda, birçok farklı sensör veya cihaz aracılığıyla gerçekleştirilebilir. Sıcaklık, basınç, hız ve hareket sensörleri gibi sensörler, PLC'ler tarafından kolayca okunabilen analog veya dijital sinyalleri üretebilir.
Veri işleme, toplanan verileri daha yararlı ve anlamlı bir formata dönüştürmek için kullanılır. PLC'ler tarafından gerçekleştirilen birçok veri işleme algoritması mevcuttur. Bu algoritmalar, verileri mantıksal veya sayısal işlemlerle işleyebilir, veri tabanı oluşturma ve veri yönetimi işlemlerini gerçekleştirebilir.
Veri analizi, toplanan verileri daha anlamlı hale getirmek için kullanılır. Bu, veri kümeleme teknikleri, regresyon analizi, yapay sinir ağları ve makine öğrenmesi gibi araçlar ve yöntemler kullanılarak gerçekleştirilebilir. PLC sistemleri, endüstriyel verilerin analizi ve öngörülebilir bakımın yapılması için son derece yararlı göstergeler sağlayabilir.
Sonuç olarak, programlanabilir mantık kontrolleri (PLC'ler), veri toplama, işleme ve analizi için mümkün olan en iyi platformlardan biridir. Endüstriyel ortamlarda bu üç sürecin etkin bir şekilde gerçekleştirilmesi otomasyon süreçlerinin kontrolünün yanı sıra verimliliğin arttırılmasına da yardımcı olacaktır.
Veri Toplama Sensörleri
PLC sistemleri ile veri toplama ve analizi yaparken kullanılan sensörlerden en yaygın olanları sıcaklık, basınç, hız, ve hareket sensörleridir.
Sıcaklık sensörleri kullanılan malzemelerin sıcaklığını ölçmek için kullanılır. Buhar, gaz ve sıvıları da ölçme yeteneğine sahiptirler. Basınç sensörleri sıvılar veya gazların basıncını ölçmek için kullanılır. Hız sensörleri eksenel, göreceli ve mutlak hızları ölçebilir. Hareket sensörleri ise nesnelerin ivmesini, yönünü ve pozisyonlarını algılayabilir.
Sensörlerin seçiminde performans, hassasiyet ve doğruluk kriterleri incelenerek en uygun sensörün seçilmesi önemlidir. Sensörlerin en doğru ve istikrarlı ölçüm yapabilmesi için doğru pozisyonlandırılması ve kalibre edilmesi gerekir. Bu nedenle sensörlerin hatası, hassasiyeti, ölçüm aralığı ve sesli/video uyarı özellikleri gibi faktörler de dikkate alınarak seçilmelidir.
- Sıcaklık sensörleri: termokupl, RTD (dirençli sıcaklık cihazı), termistörler
- Basınç sensörleri: manometre, diferansiyel basınç sensörü, piezoelektrik sensörler
- Hız sensörleri: manyetik alan sensörü, Doppler hız ölçer, lazer hız sensörü
- Hareket sensörleri: ivmeölçer, gyro, manyetik sensörler
Veri toplama sensörleri seçimi, özellikleri ve kullanım alanları doğru belirlendiğinde; PLC sistemleri ile daha verimli, etkili ve güvenli bir veri toplama ve analiz süreci gerçekleştirilebilir.
Veri İşleme Algoritmaları
Veri toplama ve işleme, endüstriyel uygulamalar için kritik bir rol oynar. Veri işleme algoritmaları, toplanan verilerin doğru, hızlı ve etkili bir şekilde işlenmesine yardımcı olur. Bu algoritmalar, verileri belirli bir formatla işlemek için kullanılan yöntemlerdir.
Mantık, en temel veri işleme algoritmasıdır. Bu algoritma, belirli bir dizi işlemin yapılması gereken bir sorunu çözmenin en basit yolu olarak tanımlanabilir. Mantık, çeşitli matematiksel operasyonları kullanan bir işlemciye sahiptir. Dolayısıyla, basit bir sorunun çözüme kavuşturulması için kullanılır.
Sayısal işlem aritmetiği, sayısal verilerin hesaplanmasında kullanılan bir veri işleme algoritmasıdır. Araç olarak, sayısal verilerin işlenmesinde kullanılan elektronik hesap makinelerinin mantığına benzer. Sayısal işlem aritmetiği, sayısal işlemlerin yapılabilmesi için gereken araçları sağlar.
Veri tabanı oluşturma, verilerin saklanması ve düzenlenmesi için önemlidir. Veri işleme algoritmaları, verileri belirli bir veritabanına kaydeder ve daha sonra bu verilerin kolayca erişilmesine ve işlenmesine izin verir. Veri tabanı oluşturma, verilerin düzenlenmesini ve işlenmesini daha kolay hale getirir.
Veri yönetimi, büyük veri kümelerinin yönetilmesinde kullanılan bir veri işleme algoritmasıdır. Veri yönetimi, verileri düzenlemek, saklamak, yüklemek, sorgulamak ve analiz etmek için bir dizi aracı kullanır. Bu algoritma, belirli bir sorunun çözülmesinde kullanılan tüm verilerin yönetimini ele alır.
Sonuç olarak, veri işleme algoritmaları, endüstriyel verilerin doğru bir şekilde toplanması, düzenlenmesi, saklanması ve analiz edilmesi için önemlidir. Her bir algoritma, farklı bir amaç için kullanılır ve her biri güçlü performans kriterleri sağlar. Bu nedenle, doğru veri işleme algoritması seçimi büyük önem taşır.
Veri Analizi Araçları ve Yöntemleri
Veri analizi, işletmeler için büyük bir avantaj sağlayabilir. Veri kaynaklarından yararlanarak gelecekteki trendleri tahmin etmek, müşteri davranışlarını analiz etmek veya verimlilik artışı sağlamak mümkündür. Ancak verileri analiz etmek için doğru araçları kullanmak ve doğru yöntemleri bilmek önemlidir.
Regresyon analizi, bir bağımlı değişken ile bir veya daha fazla bağımsız değişken arasındaki ilişkiyi belirlemek için kullanılan bir istatistiksel analiz yöntemidir. Bu analiz, bir şirketin ürün satışlarındaki artışı veya azalışı, belirli aralıklarda müşteri sayısında meydana gelen değişiklikleri veya bir ürünün fiyatındaki dalgalanmaları tahmin etmek için kullanılabilir.
Veri kümeleme, benzer özelliklere sahip verileri küçük gruplar halinde sınıflandırmak için kullanılan bir methoddur. Bu, belirli bir hedefe yönelik olarak verileri anlamak için yararlı olabilir. Örneğin, müşterilerin alışveriş davranışlarını anlamak veya bir şirketin çalışanlarının performansını incelemek için verileri kümeleme yöntemi kullanılabilir.
Yapay Sinir Ağları, öğrenme ve hafıza işlemleri için biyolojik sinir ağlarından esinlenerek geliştirilmiştir. Bu analiz yöntemi, bir şirketin finansal verilerindeki düzenlilikleri, ürün kalitesini ve müşteri sadakatini incelemek için kullanılabilir.
Makine öğrenmesi, bilgisayarların verileri analiz etmek ve öğrenmek için kullanabileceği bir mekanizmadır. Bu analiz yöntemi, geniş veri kümelerini anlamak ve gelecekteki trendleri tahmin etmek için kullanılabilir. Örneğin, bir şirketin gelecekteki satış tahminlerini veya bir kullanıcının tercihlerini anlamak için makine öğrenmesi algoritması kullanılabilir.
Veri analiz araçları ve yöntemleri sayesinde, işletmeler daha verimli hale gelebilir ve daha büyük başarılar elde edebilirler. Doğru araçları seçmek ve doğru metodolojileri kullanmak, şirketler için önemli bir fark yaratabilir ve rekabet avantajı sağlayabilir.