Makine tasarımında performansın artırılması için enerji verimliliği, malzeme kullanımı optimizasyonu ve mekanik verimlilik iyileştirmesi gibi yöntemler kullanılabilir Enerji verimliliği iyileştirmesi için verimli motor kullanımı, enerji tüketimi analizi, aydınlatma kontrolü ve enerji geri kazanımı gibi yöntemler kullanılabilir Malzeme kullanımı optimizasyonu için ise malzeme seçimi ve tasarım optimizasyonu önemlidir Metal malzemeler arasında çelik, alüminyum ve demir, polimer malzemeler arasında ise polimetil metakrilat ve polikarbonat gibi seçenekler bulunmaktadır Tasarım optimizasyonu için bilgisayar destekli tasarım ve sonlu elemanlar analizi kullanılabilir
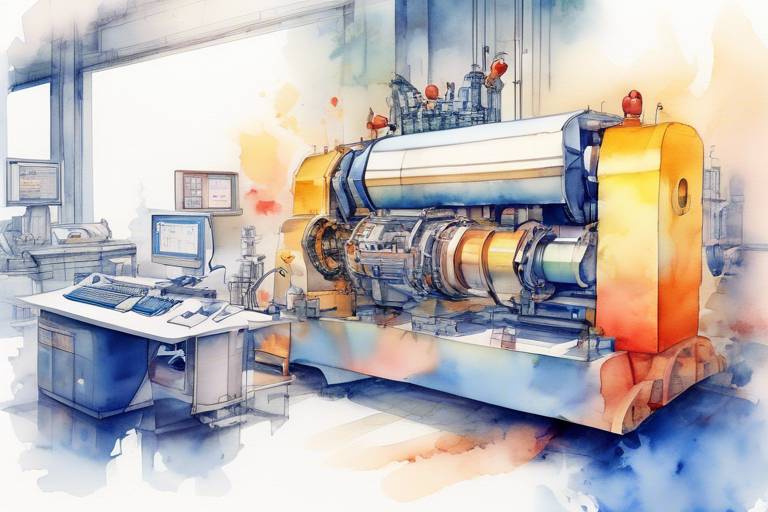
Makine tasarımında performansın artırılması, akıllı tasarımlar ve gelişmiş teknolojilerin kullanılması ile mümkündür. Enerji verimliliği iyileştirme, malzeme kullanımı optimizasyonu ve mekanik verimlilik iyileştirmesi bu popüler yöntemlerden bazılarıdır.
Enerji Verimliliği İyileştirmesi
Makine tasarımcıları, enerji verimliliğini arttırmanın birçok yolu olduğunu biliyorlar. Bunlardan biri, makinenin daha az enerji harcamasını sağlamak için gerekli olan enerji tüketimini azaltmaktır. Bu amaçla, enerji verimliliğini artırmaya yardımcı olan yöntemler kullanılır. Bunlar arasında, verimli motor kullanımı, enerji tüketimi analizi, aydınlatma kontrolü ve enerji geri kazanımı sayılabilir.
Bunun yanı sıra, tasarımcılar enerji kaynaklarını daha verimli bir şekilde kullanarak enerji verimliliğini artırabilirler. Bu amaçla, yüksek verimli ekipman ve yenilenebilir enerji kaynakları gibi teknolojiler kullanılabilir. Böylece, elektrik faturası maliyetleri azaltılarak ürün performansı arttırılabilir.
Ayrıca, enerji verimliliği hakkında bilgi sahibi olan personelin eğitimi ve farkındalık yaratmak da önemlidir. Bu sayede, enerji verimliliği sağlamak için ihtiyaç duyulan adımların farkına varılır ve enerji tasarrufu bilinci oluşturulur.
- Verimli motor kullanımı
- Enerji tüketimi analizi
- Aydınlatma kontrolü
- Enerji geri kazanımı
- Yüksek verimli ekipman kullanımı
- Yenilenebilir enerji kaynakları
- Personel eğitimi ve farkındalık yaratmak
Malzeme Kullanımı Optimizasyonu
Makine tasarımcıları, daha dayanıklı ve hafif makine parçaları üzerinde çalışarak ürün performansını maksimum seviyeye çıkarmaya çalışıyorlar. Bu amaçla, malzeme seçimi ve tasarım optimizasyonu çok önemlidir. Malzemelerin özellikleri incelenerek en uygun malzeme seçilmeli ve bu malzemelerin tasarımı optimize edilmelidir.
Malzeme seçimi yaparken çelik, alüminyum, demir gibi metal malzemeler veya hafif ve güçlü polimer malzemeler tercih edilmektedir. Her malzemenin farklı avantajları ve dezavantajları bulunmaktadır. Tasarım optimizasyonu için ise bilgisayar destekli tasarım ve sonlu elemanlar analizi kullanılmaktadır.
Bir başka konu ise malzemelerin geri dönüştürülebilirliği ve çevreye olan etkisidir. Bu nedenle, çevre dostu malzemeler ve malzeme geri dönüşümü de tasarımda düşünülmelidir.
Malzeme Seçimi
Makine tasarımcıları, farklı malzemelerin özelliklerini analiz ederek en iyi seçimi yapmaya çalışırlar. Farklı malzemelerin çeşitli avantajları bulunmaktadır. Metal malzemeler, yüksek dayanıklılık ve mukavemet özellikleri nedeniyle sıklıkla kullanılır. Çelik, alüminyum ve demir gibi metal malzemeler, farklı endüstrilerde çeşitli uygulamalarda kullanılabilir.
Polimer malzemeler ise, hafif ve güçlüdür ve sertleştiricilerle birlikte kullanıldıklarında dayanıklılık sağlarlar. Polimetil metakrilat (PMMA) ve polikarbonat (PC) gibi polimer malzemeler, birçok endüstride kullanılır. Cam elyafı takviyeli plastikler, dayanıklılık ve mukavemeti artırmak için kullanılan bir diğer polimer malzeme türüdür.
Metal Malzemeler
Metal malzemelerin kullanımının yaygın olmasının sebebi, mukavemeti ve dayanıklılığı ile bilinmeleridir. Çelik, alüminyum ve demir, makine tasarımında en sık kullanılan metal malzemelerdir. Çelik, dayanıklılık ve mukavemeti ile ön plana çıkar ve aynı zamanda ekonomik bir seçenektir. Alüminyum, hafif olması ve korozyona dayanıklı olması sebebiyle tercih edilir. Demir ise, kolay işlenebilir olması, mukavemeti ve uygun fiyatı sebebiyle kullanılır.
Metal malzemelerin seçiminde malzemenin kullanım amacı, mekanik özellikleri, üretim yöntemi, fiyatı ve sertliği gibi faktörler etkili olmaktadır. Genel olarak, mukavemeti ve dayanıklılığı yüksek olan metal malzemeler, makine tasarımında sıklıkla tercih edilen malzemelerdir.
- Çelik: Dayanıklılığı ve mukavemeti ile öne çıkan çelik, ekonomik bir seçenektir.
- Alüminyum: Hafif oluşu ve korozyona dayanıklı olması sebebiyle tercih edilir.
- Demir: Kolay işlenebilir olması, mukavemeti ve uygun fiyatı sebebiyle kullanılır.
Polimer Malzemeler
Polimer malzemeler, sentetik polimerlerin üretilmesiyle elde edilir. Bu nedenle, özellikleri malzemelerin üretiminde kullanılan monomerler ve polimerizasyon sürecine bağlıdır. Polimer malzemeler, ağırlıklı olarak hafif ve Güçlüdür, bu nedenle birçok endüstride yaygın olarak kullanılır.
Bu malzemeler, ayrıca kolay işlenebilir ve şekillendirilebilir, neme karşı dirençlidir ve kimyasal dayanıklılık gösterir. Polimerler, maliyetleri nedeniyle metal ve diğer malzemelerin yerini almaya başlamıştır. Polimerleri kullanmak, ayrıca parçaların ağırlığını ve maliyetini azaltır, böylece daha yüksek performans, düşük maliyet ve daha uzun ömür kombinasyonu elde edilir.
Polimer malzemelerin avantajlarına örnek olarak, yüksek kimyasal dayanıklılık, yüksek aşınma ve sertlik direnci gösterilebilir. Ayrıca, polimer malzemeler sıcaklık ve korozyona karşı dayanıklıdır ve elektrik yalıtımı özelliklerine sahiptir. Farklı polimer türleri, farklı özellikler gösterir, bu nedenle uygulanacak kullanım yerine ve tasarım özelinde dikkatle seçilmesi gerekir.
Tasarım Optimizasyonu
Tasarım optimizasyonu, makine tasarımında uygulanan bir yöntemdir. Bu yöntem, tasarımın optimize edilmesi yoluyla makine performansının artırılmasını sağlar. Tasarım optimizasyonu için birçok teknik kullanılabilir. Bu teknikler arasında, bilgisayar destekli tasarım ve sonlu elemanlar analizi gibi yöntemler yer alır. Bilgisayar destekli tasarım, makine parçalarının tasarlanması için kullanılan bir tekniktir. Bu yöntem, bilgisayar programları kullanılarak parçaların tasarımı gerçekleştirilir. Sonlu elemanlar analizi ise, makine parçalarının gerilim ve deforme durumlarının analiz edilmesi için kullanılan bir tekniktir. Bu yöntem sayesinde, parçaların daha etkili tasarımlarının yapılması sağlanır.
Bilgisayar Destekli Tasarım
Bilgisayar destekli tasarım programları, makine parçalarının 3D modellerinin oluşturulması ve tasarımın optimize edilmesi için kullanılır. Bu programlarda, tasarımın mekanik özellikleri, yapısal analizi ve prototip üretimi yapılabilmektedir. Bilgisayar destekli tasarım programları, tasarım sürecinde zaman ve maliyet tasarrufu sağlamakta ve üretim sürecinde hataların azalmasını sağlamaktadır.
Bazı popüler bilgisayar destekli tasarım programları arasında AutoCAD, SolidWorks ve CATIA bulunmaktadır. Bu programlar, mühendislerin parça tasarımlarını oluşturması ve mekanik özelliklerini analiz etmesi için kullanılan birçok özellik sunmaktadır. Ayrıca, programlar arasında dosya aktarımı da kolaydır, böylece farklı programlar kullanan mühendisler aynı tasarım üzerinde çalışabilirler.
Sonlu Elemanlar Analizi
Sonlu elemanlar analizi, makinelerin tasarım optimizasyonu için son derece önemlidir. Bu yöntem, bir makine parçasının gerilim ve deforme durumlarının detaylı analizini yapar ve bu analiz sonuçlarına göre tasarım iyileştirmesi yapılmasına imkan tanır.
Sonlu elemanlar analizi, birçok farklı mühendislik alanında kullanılmaktadır. Bu analiz yöntemi, hem mekanik hem de termal yükleme altında çalışan makine parçalarının davranışlarının analiz edilmesine imkan tanır.
Bu analiz yöntemi ile, makine parçaları için en uygun boyut, şekil ve malzeme seçimi gibi faktörler göz önünde bulundurularak optimizasyon yapılabilir. Sonlu elemanlar analizi sonuçları, tasarımcılara, makinelerinin performansını artırmak için nasıl değişiklikler yapabilecekleri konusunda yol gösterir.
Sonlu elemanlar analizi, makinelerin yapısal bütünlüğünü bozmadan tasarımın optimize edilmesine olanak tanır. Bu yöntem sayesinde, makinelerin daha verimli, daha dayanıklı ve daha güvenli olması sağlanır.
Mekanik Verimlilik İyileştirmesi
Parçaların mekanik verimliliğini artırmak için birçok yöntem mevcuttur. Bunlar arasında, sürtünmeyi azaltma teknikleri, doğru aktarma organlarının kullanımı ve parça geometrisinin optimize edilmesi sayılabilir. Sürtünmeyi azaltmak için sıvıları kullanmak, sürtünme azaltıcı kaplamalar uygulamak ve yüzey pürüzlülüğünü azaltmak gibi teknikler kullanılabilir. Doğru aktarma organlarının seçimi de mekanik verimliliği artırmak için önemlidir. Variomatik şanzımanlar ve kayış tahrikleri, verimli bir aktarım sağlayarak performans artışına yardımcı olabilirler. Son olarak, parça geometrisinin optimize edilmesi de mekanik verimliliğin artırılması için bir yöntemdir. Bu, malzeme kullanımının optimize edilmesi, ağırlık azaltma ve sürtünme azaltıcı tasarımları içerebilir.
Sürtünme Azaltma
Makine tasarımcıları, performansı artırmak için sürtünmeyi azaltan teknikler kullanmaktadırlar. Sürtünme azaltma, enerji tasarrufunun yanı sıra, makine parçalarının ömrünü de uzatmaktadır. Bununla birlikte, sürtünmeyi azaltmanın birçok yolu vardır ve makinelerin özelliklerine göre farklı teknikler kullanılabilir.
Birinci yöntem, sıvıların kullanımıdır. Yağlama ve soğutma sıvıları, makine parçalarının yüzeyinde sürtünmeyi azaltmak için kullanılabilir. Seramik kaplamalar gibi yüksek teknoloji ürünleri de kullanılabilir. İkinci yöntem ise, sürtünme azaltıcı kaplamalardır. Bu kaplamalar, parçaların yüzeyine uygulanır ve sürtünme oranını azaltır. Üçüncü yöntem ise, doğru aktivasyon parçalarının seçimidir. Yanlış aktarma parçaları sürtenme artışına neden olabilir. Kayış tahrikleri ve variomatik şanzımanlar, uygun aktarma organlarının seçilmesinde popüler olan yöntemlerdir.
Sıvıların Kullanımı
Sıvıların kullanımı, makine performansını arttırmak için önemli bir yöntemdir. Bu yöntem, sürtünme azaltma için kullanılan bir tekniktir. Yağlama sıvıları, parçaların üzerindeki sürtünmeyi azaltmak ve aşınmayı önlemek için kullanılır. Performansı artırmak için, makine tasarımcıları doğru yağlama sıvılarını seçmeye özen göstermelidirler.
Soğutma sıvıları ise, makinedeki ısıyı azaltmak ve performansı artırmak için kullanılır. Yüksek sıcaklıklar, parçaların ömrünü azaltabilir ve performansı düşürebilir. Bu nedenle, makine tasarımcıları, uygun soğutma sıvıları seçerek makinedeki ısıyı kontrol altında tutmaya çalışırlar.
Bunun yanı sıra, yağlama ve soğutma sıvılarının doğru şekilde kullanılması da önemlidir. Yanlış kullanım, parçaların performansını olumsuz etkileyebilir ve hatta hasara neden olabilir. Makine tasarımcıları, sıvıların doğru kullanımı ve bakımı hakkında bilgi sahibi olmalıdırlar.
Tüm bunların yanı sıra, bazı makinelerde farklı sıvıların bir arada kullanılması gerekebilir. Bu durumlarda, sıvıların uyumlu olması ve birbirleriyle etkileşime girmemesi önemlidir. Makine tasarımcıları, uyumlu sıvıları seçerek makine performansını arttırmayı hedeflemelidirler.
Sürtünme Azaltıcı Kaplamalar
Sürtünme azaltıcı kaplamalar, makine parçalarının yüzeylerine uygulanarak sürtünmeyi azaltır. Bu sayede parçaların ömrü uzar, enerji tasarrufu sağlanır ve performans artırılır. Sürtünme azaltıcı kaplamalar genellikle polimer veya seramik malzemelerden yapılmıştır.
- Polimer Kaplamalar: Polimer kaplamalar, sürtünmeyi azaltan ve aşınmayı önleyen bir tabaka oluşturur. Polimer kaplamaların avantajları arasında hafiflik, dayanıklılık ve çevre dostu olması yer alır.
- Seramik Kaplamalar: Seramik kaplamalar, yüksek sıcaklık ve basınca dayanabilen bir tabaka oluşturur. Seramik kaplamaların avantajları arasında yüksek sıcaklıkta çalışan makineler için uygun olması ve aşınmaya dayanıklı bir tabaka sağlaması yer alır.
Sürtünme azaltıcı kaplamalar, farklı uzmanlık alanlarına sahip mühendisler tarafından özel olarak tasarlanır. Bu sayede, kaplamaların performansı ve kalitesi artırılabilir. Makine tasarımında sürtünmeyi azaltmak için sürtünme azaltıcı kaplamalar kullanmak önemlidir.
Verimli Aktarma Organları Kullanımı
Aktarma organları, makine performansını önemli ölçüde etkileyen bir unsurdur. Doğru aktarma organının seçimi, makine tasarımında performansın artırılması için büyük önem taşır. Aktarma organları, mekanik verimliliği artırarak enerji tasarrufu sağlayabilir ve sürtünmeyi azaltarak aşınmayı azaltabilir. Doğru aktarma organlarının seçimi, özellikle makine parçalarının aşırı yüklenmesi durumunda önemlidir.
Birçok farklı aktarma organı türü vardır ve doğru seçim, özellikle makine performansının artırılması hedeflendiğinde kritik öneme sahiptir. Örneğin, kayış tahrikleri yüksek oranda esneklik sağlayarak titreşimi önlerken, variomatik şanzımanlar yüksek hızlarda verimli bir aktarım sağlar.
Özellikle yüksek performanslı makineler için, doğru aktarma organının seçimi, makinelerin daha uzun ömürlü olmasına ve daha az bakım gerektirmesine yardımcı olabilir. Makine tasarımında performansın artırılması için doğru aktarma organlarının seçimi, özellikle maliyet düşürmek gibi diğer hedeflerle birlikte düşünüldüğünde, kritik bir faktördür.
Variomatik Şanzımanlar
Variomatik şanzımanlar, modüler bir tasarım ile otonom değişken oranlı şanzımanlardır. Bu şanzımanlar, motor hızını bir değişken oranlı kayış ve konik vidalar kullanarak değiştirir. Bu sayede, daha verimli bir aktarım sağlanır ve yakıt tüketimi azaltılır. Bunun yanı sıra, sürtünme kaynaklı kayıpların en aza indirilmesi sayesinde, daha yüksek bir hızlanma ve daha düşük bir RPM seviyesi de elde edilebilir.
Bununla birlikte, variomatik şanzımanların bazı dezavantajları da bulunmaktadır. Yüksek RPM'lerde ses seviyesi artar ve sınırlı bir maksimum tork üretimi vardır. Ayrıca, daha yüksek hızlarda, kayışın ısınması ve ömrünün azalması gibi sorunlar oluşabilir.
Variomatik şanzımanların avantaj ve dezavantajları göz önünde bulundurulduğunda, tasarımın uygulanacağı amaç göz önünde bulundurularak bu şanzımanın kullanılması kararlaştırılmalıdır.
Kayış Tahrikleri
Kayış tahrikleri, birçok endüstride yaygın olarak kullanılan bir aktarma organıdır. Bu tahrikler, bir motor tarafından üretilen gücü, diğer bir makine parçasına iletmek için kullanılır. Kayış tahriklerinin en büyük avantajı, düşük maliyete sahip olması ve kolay montaj edilebilmesidir. Ayrıca, kayış tahrikleri, yüksek momentlerin aktarılmasına da izin verir.
Kayış tahriklerinin bazı dezavantajları da vardır. Örneğin, kayışların yüksek hızlarda kayması olasılığı vardır, bu nedenle çekiş kayışları sık sık değiştirilmelidir. Ayrıca, kayış tahrikleri, aşırı yük altındayken gürültü yapabilirler ve titreme problemleri yaşayabilirler.